Improved Flux-Cored Welding for Heavy-Duty Field Use
Understanding operator challenges is what drives innovation in the welding industry. For some, that challenge is outdoor welding, where using shielding gas is not optimal. In these extreme conditions, traditional MIG welding won’t necessarily work. Turning to a different process, such as self-shielded flux-cored welding (FCAW-S), allows for more effective welding in the field. When welding in harsh environments, operators require durable, rugged equipment that can withstand the elements and the nature of the work.
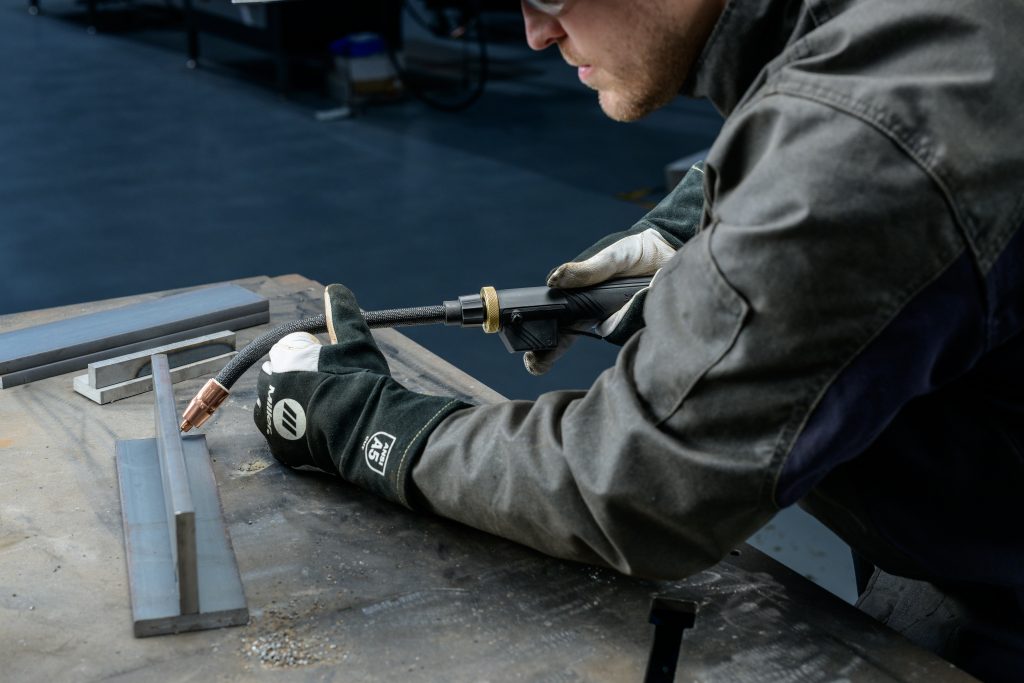
Operators utilizing self-shielded flux-cored welding demand a high level of flexibility and reliability in their equipment, which is why Bernard optimized the IronPro™ self-shielded FCAW gun to be extremely durable when welding in heavy-duty field operations.
Features that enhance flux-cored welding for heavy-duty applications
Operators need a gun that stays cooler in the hand and is lightweight, portable and reliable — handling the rigor of the toughest worksites while improving operator comfort. To improve usability and the overall user experience, IronPro introduces several enhancements to meet those needs and help overcome technical and operational challenges when out in the field.
Specifically, the IronPro 350 has a 350-amp rated output with a 60% duty cycle, making it ideal for operators working in construction, shipbuilding and heavy manufacturing. The design was further updated to include:
- Interchangeable neck options: The IronPro 350 features two rotatable neck options — one that’s 7 inches with a 60-degree bend radius and one that’s 12 inches with a 45-degree bend radius. These allow operators to ergonomically access even the most challenging, out-of-position welds. The neck can be rotated for a trigger-on-top approach, allowing for even more dexterity and customization at the joint.
- Sealed trigger: The trigger is designed to keep the area slag- and spatter-free, reducing maintenance downtime. Being non-metallic, it absorbs less heat, and it’s made with a sealed switch that helps keep out dust and dirt, leading to a longer lifespan.
- Lighter cable: The weight and bulk of higher amperage gun cables can lead to fatigue over extended periods of time. The cable for the 350 is lighter, making it more mobile and user-friendly for a welder on a day-to-day basis.
Incorporating all the updated design features mentioned above, IronPro 450 is also available for higher amperage applications, supporting up to 3/32″ wire size. IronPro 450 has a 450-amp-rated output with a 60% duty cycle.

Additional ways to improve field performance
To keep operators welding in tight positions longer, using AccuLock™ S consumables will increase contact tip life, resulting in fewer tip changes and increased overall performance with fewer points of failure. To further improve field performance, the cable liner incorporates Bernard® E-Z Feed™ technology, ensuring a reliable and smooth feed, minimizing chatter and poor arc characteristics. The superior feeding performance, paired with high-quality consumables, leads to more consistent welds, minimizing rework.
The tip insulator was redesigned to be more durable, withstanding more aggressive weld parameters to keep the electricity from short-circuiting between the tip and neck. Additionally, the insulator transitioned from being a slip-on to a thread-on, allowing it to stay in place better. These design improvements help minimize bridging from spatter and improve operator safety by ensuring the contact tip remains isolated to allow current to flow correctly through the wire to the weld puddle. Operators can choose between composite tip insulators, for increased joint access, or armored tip insulators, which are well-suited for higher amperage applications. These options allow operators to better customize their IronPro to suit the needs of their applications.

When welding heavy-duty applications in the field, operators need power, durability and consistency. The IronPro 350 offers improvements that exceed those demands. Welders can elevate their welding performance — and experience the productivity and quality benefits self-shielded flux-cored welding offers.
4 Reasons Genuine Consumables Lead to Better MIG Welds
4 Reasons Genuine Consumables Lead to Better MIG Welds
Welders must be able to rely on every aspect of their equipment, and consumables are an integral component of a high-quality weld. When you notice an uptick in downtime and consumables consumption, it’s time to take a deeper look at what the culprit could be. An easy place to start is by looking at the quality of the consumables you’re using. Lower-quality consumables can lead to major expenses in the long run — as seen in lost production, weld rework and the cost of constant replacements.
Original equipment manufacturer (OEM) consumables are the right choice for improved operations and consistent, high-quality welds. Below are four reasons you should consider investing in genuine consumables over lower-quality options.

- Consumable quality affects your performance
Even the best MIG guns or the most highly trained operators cannot offset the impact of poorly made consumables on performance. OEM consumables are manufactured using high-quality materials, which helps deliver the arc stability needed to create smooth, even welds with minimal defects. In addition to helping improve weld integrity and facilitating more durable weld joints, genuine consumables also help prevent excessive spatter and minimize post-weld cleanup.
Because OEM consumables are manufactured for reliability, they have consistent diameters and surface conditions that ensure smoother feeding through the gun. By contrast, non-genuine consumables are often made from low-quality materials and may not consistently meet key manufacturing specifications.
2. OEM consumables are expertly designed to be reliable
Genuine consumables are backed by research, technology and expertise, having been produced to ensure the material composition and mechanical properties are consistent and reliable. Keeping those details at the forefront makes for stable arcs, high-quality welds, fewer points of failure and simplified maintenance. Their ease of use can even help to reduce welder training times and shorten your troubleshooting list if problems do arise.

Copycat manufacturers are also less likely to submit their consumables to the rigorous testing and quality assurance processes that OEMs follow.
AccuLock ™ consumables have been designed to flawlessly integrate into Bernard® semi-automatic and Tregaskiss® fixed automatic and robotic MIG welding guns and to address welders’ most common pain points.
For semi-automatic MIG welding applications, the AccuLock™ S consumables system paired with front load E-Z Feed™ liners reduces liner trim length errors and erratic wire feeding while simultaneously increasing contact tip life. The front load liners are locked and concentrically aligned to both the contact tip and power pin. This eliminates misalignment and provides a flawless wire feed path, ensuring uninterrupted delivery of the wire to the weld puddle. As a result, operators have fewer burnbacks, bird nests and erratic arcs.
The AccuLock R consumables system is available for robotic or fixed automatic MIG welding applications. With these consumables, operators have the opportunity to realize significant improvements, like increasing contact tip life span and decreasing issues with contact tip cross-threading.
For operations constantly managing complex or costly consumables inventories, AccuLock S and AccuLock R consumables systems share a common contact tip — making for simplified part inventory across mixed fleets of semi-automatic and automated welding applications. Operations who are looking to get more life out of their consumables but aren’t using Bernard or Tregaskiss guns can purchase the conversion series consumables to still experience the benefits of a high-quality system.
3. Using low-quality products limits your manufacturer’s ability to help
A good OEM is invested not only in the performance of its products but also in the overall user experience, which extends to customer service. Reputable OEMs usually have expert technical support teams that help with troubleshooting and provide solutions if something goes wrong. They can also share product tips and offer advice, like how to make your MIG gun consumables last longer.

However, if you’re using nongenuine consumables and parts, technical support teams are unable to offer such assistance. Often, if an issue arises involving lower-quality parts, it will be essential to order genuine parts and wait for them to arrive to see if the issue still occurs before the OEM team can offer support. Using genuine parts from the get-go means you can get expert advice right away — or avoid issues altogether.
4. OEM products can have a longer life
Because OEMs are making greater investments in materials, design and testing, that means OEM consumables usually cost more than low-quality consumables. But, as the saying goes, you get what you pay for. Consumables are probably not your biggest cost — labor is. So any money you save by using cheaply made consumables could be offset by the extra labor required to frequently change tips, troubleshoot equipment failure or rework a faulty weld. Those looking for superior performance and longevity find that OEM options can equate to more arc-on time — and more products out the door.
AccuLock contact tips are designed so that 60% of the tip is buried within the diffuser for less exposure to the heat of the arc and more cooling from shielding gas. This gives the tip a life that can be two to three times longer than other tips.
All told, because genuine consumables are designed specifically for your MIG welding gun, they can last longer, be more reliable and deliver higher-quality welds — ultimately enhancing the operator experience and your welding operation’s bottom line.
Mastering MIG welding with adjustments, equipment and techniques
Mastering MIG welding with adjustments, equipment and techniques
Discover essential adjustments, equipment tips, and expert techniques to accelerate your MIG welding game by reading our article in the October issue of The Welder. You’ll learn how to balance voltage and wire feed speed for flawless welds, select the right welder and shielding gas, and master gun angle and travel speed. Plus, we’ll guide you through troubleshooting common challenges to ensure consistent, high-quality results. Don’t miss out on transforming your welding skills—dive into the full article now!
Introducing The Bernard® Clean Air E™
Introducing The Bernard® Clean Air E™
Welding professionals face daily challenges in keeping their work environment clean and safe. With strict weld fume regulations, effective fume control is more important than ever. The Bernard® Clean Air E™ fume extraction MIG gun helps by capturing welding fumes directly at the source without sacrificing performance.
Why Source Capture Matters
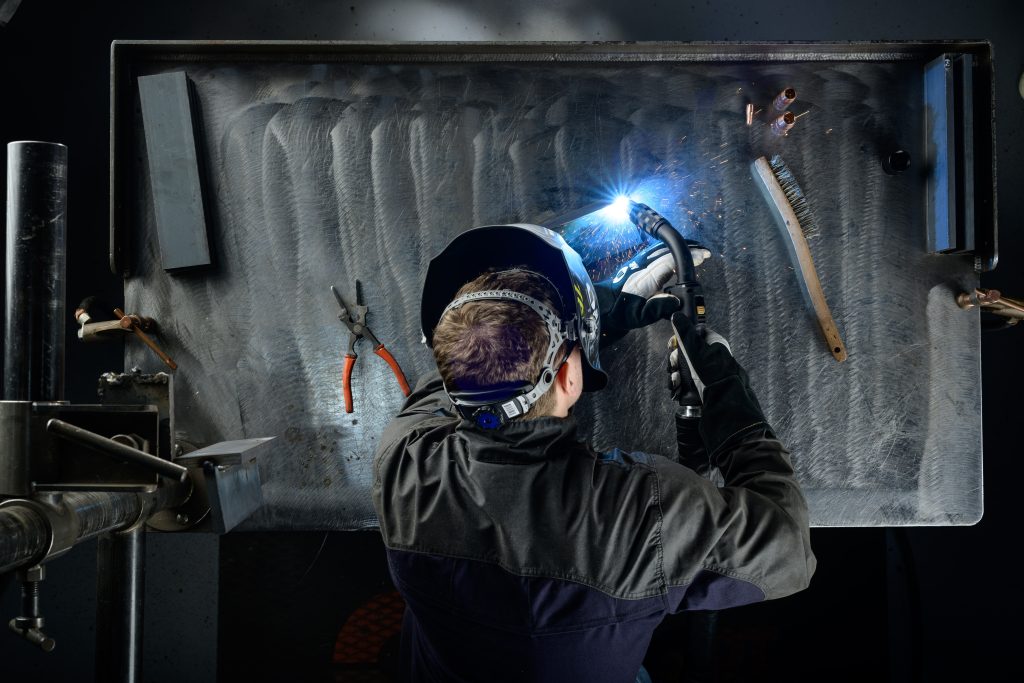
Capturing weld fume as close to the point of generation as possible, also known as source capture, is one of the most effective ways to reduce exposure. Unlike general ventilation or ambient air systems that dilute fumes, source capture methods like fume extraction guns immediately remove hazardous particles, helping improve air quality for operators and surrounding workers.
The Clean Air E™ captures up to 95% of fume at the source. The gun is built with adjustable extraction control through interchangeable shroud lengths and a slider allowing operators to fine-tune suction levels without affecting shielding gas coverage. This balance is critical for maintaining weld quality while maximizing fume capture.
Key Benefits of the Clean Air E™
Efficient Extraction
By removing up to 95% of fumes directly at the arc, the Clean Air E™ helps reduce exposure risks and contributes to a cleaner workspace.
Enhanced Ergonomics
With a lightweight handle design, the Clean Air E™ allows you to weld longer without fatigue. The ball swivel at the rear of the handle makes maneuvering easier, even in difficult positions.
Engineered for Endurance
This fume gun is built to withstand the toughest working environments. Made from durable, tested materials, it features a robust and straightforward design for easy maintenance.
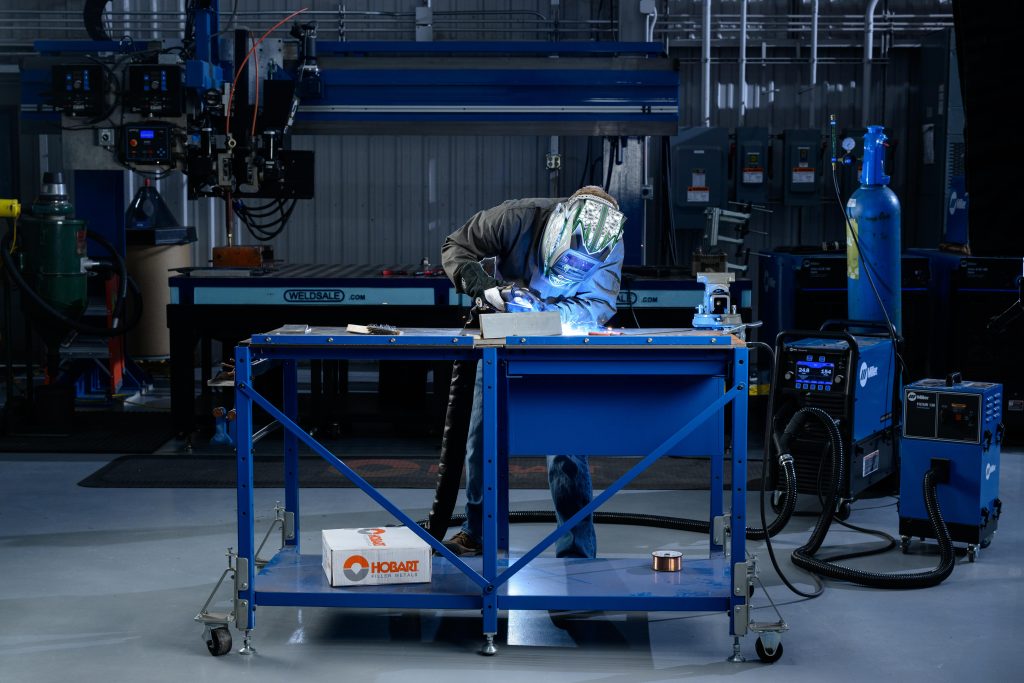
Designed for Demanding Applications
Ideal for high-amperage and high-deposition rate applications, the Clean Air E™ is well-suited for industries such as: Shipbuilding, Heavy equipment manufacturing, General fabrication and manufacturing
Ergonomic and Easy to Use
Unlike bulky ventilation systems, fume extraction guns like the Clean Air E™ seamlessly integrate into a welder’s workflow. With a lightweight, ergonomic design and a user-friendly adjustment slider on the guns handle, it operates much like a standard MIG gun while providing the added benefit of fume extraction.

Customizable
We know every welder has their own preference when it comes to welding style. That’s why we designed two trigger options—a button and a lever, plus an extended lever for added comfort. We also made the shrouds interchangeable, offering three lengths to optimize either weld visibility or fume extraction, depending on your application.
A Smarter Step Toward Safer Welding
No single solution eliminates all welding fume exposure, but using a fume extraction gun alongside a compatible extraction unit like the Miller® Filtair®215 can significantly improve a workplace environment. The Bernard® Clean Air E™ provides a practical, effective way to prioritize welder safety and performance.

It starts at the source™
For Immediate Release BEECHER, Ill./WINDSOR, Ontario (March 20, 2025) — Bernard announced the release of the new Clean Air E™ fume extraction MIG gun, the newest high-efficiency fume extraction gun in the brand’s lineup. Crafted for efficient extraction, enhanced ergonomics and engineered endurance, this gun sets a new standard in MIG welding fume capture technology. With an ongoing priority to ensure safer, cleaner work environments for operators coupled with heightened fume standards being implemented across the country, Bernard saw an opportunity to evolve the standard fume extraction gun to maximize its efficiency and usability. Bernard took customer and welder feedback and designed a product that would be the most impactful for welders in a next-generation fume extraction gun. The team applied that feedback throughout the research and development process until it resulted in the Clean Air E™, which offers solutions to common operator pain points, including: · Efficient extraction: The Clean Air E™ achieves up to 95% fume capture right at the source, which improves air quality in the workspace and reduces OSHA-related risks. · Enhanced ergonomics: The ergonomic design reduces strain and fatigue on welders, which allows them to focus on precision and quality for extended use. · Engineered for endurance: The Clean Air E™ features durable components and long-life consumables, which reduces downtime and maintenance costs, delivering a lower cost of total ownership. “When it comes to welding, operators seek the trifecta in their gun: ergonomics, extraction performance and ease of maintenance,” said Jerome Parker, product manager, Bernard. “The Clean Air E™ was designed alongside actual users to ensure we arrived at a solution that redefined traditional fume capture guns for the modern welder, enhancing both their operator experience and their weld environment.” On the gun itself, the Clean Air E™ offers enhanced features for easier and more efficient use: · Improved weld access: Three nozzle shroud lengths allow operators to balance fume capture with weld access and improved visibility of the weldment. · Instant flow adjustment: The new flow control slide on the back of the handle enables welders to easily reduce airflow by up to 10 cfm to help overcome porosity issues. · Upgraded handle comfort: Two handle styles are available to suit different grip styles and hand sizes, with internals contoured to enhance airflow and fume capture. The lever trigger can also be mounted on top for additional comfort. · Increased flexibility: A durable, lightweight aluminum ball swivel at the end of the handle provides 15 degrees of extra flex in any direction for additional improved ergonomics. · Maximized airflow: A new Y-connector offers contoured internals that maximize airflow, with a vacuum outlet that is compatible with any fume extraction unit. For a premium fume extraction pairing, operators have the option to connect the Clean Air E™ to the Miller® FILTAIR® 215. Learn more about how the Clean Air E™ can deliver safety, performance and comfort for welders at https://www.startsatthesource.com/ About Bernard Bernard, a leading manufacturer of premium semi-automatic MIG welding guns and consumables, is dedicated to enhancing welding productivity and performance. Headquartered in Beecher, Illinois, Bernard is known for innovative solutions that prioritize operator comfort, ease of maintenance, and exceptional durability. Bernard is a proud brand of Illinois Tool Works Inc. (NYSE: ITW). For more information, visit BernardTregaskiss.com, call 1-855-MIGWELD (1-855-644-9353), email CS@itwmig.com. Contact: Lauren Smith, Hiebing for Bernard/Tregaskiss phone: +1 6082684408 lsmith@hiebing.com The Occupational Safety and Health Administration (OSHA) and other safety regulatory bodies set the allowable exposure limits for weld fumes and other particulates, including hexavalent chromium, with the aim of protecting employees against potential health hazards in the workplace. Providing welding operators with proper ventilation during the welding process is an important step companies can take to help meet the standards — and to help provide a safe and comfortable work environment. Companies may opt to invest in centralized fume extraction systems, which are designed to protect the entire shop area. These systems involve the installation of new ductwork and fans to remove fumes and are highly effective, but they are also more expensive than other options. A viable alternative for some companies is a fume extraction gun used in conjunction with a fume extraction device or localized filtration system. Fume extraction guns are available in a variety of amperages (typically 300 to 600), cable styles and handle designs. As with any welding equipment, they have their best applications, advantages and limitations, as well as recommended techniques for achieving the best results. Fume extraction guns operate by capturing the fume generated by the welding process right at the source, over and around the weld pool. The weld fumes removed by these guns are composed of a combination of the filler metal and base material. Various manufacturers have proprietary means of constructing guns to conduct this action, but at a basic level they all operate similarly: by mass flow, or the movement of material. A vacuum chamber suctions the fumes through the handle of the gun, into the gun’s hose and through to a port on the filtration system (sometimes informally referred to as a vacuum box). Typically, fume extraction guns are larger than regular welding guns, and include the vacuum and hose that are necessary to extract the fumes. Some manufacturers offer fume extraction guns with a vacuum hose swivel on the rear of the handle to make them easier to maneuver. Also, design advancements have minimized the handle weight and size to make the guns as light as possible for operator comfort, while still offering consistent fume extraction benefits. The Bernard® Clean Air E™ fume extraction gun is designed to efficiently capture welding fumes at the source, helping to create a cleaner work environment. This gun is particularly well-suited for applications using solid welding wire and for operations in confined spaces, where fume extraction directly in the welding operator’s breathing zone is essential. Industries that frequently benefit from this technology include shipbuilding, heavy equipment manufacturing, and general fabrication, especially when working with mild or carbon steel. Additionally, for applications in petrochemical industries or those involving stainless steel welding, where higher levels of hexavalent chromium are present, the Clean Air E™ gun provides an effective solution for improving air quality. Designed for high-amperage and high-deposition rate applications, this gun performs best in flat and horizontal welding positions, where it can effectively capture rising fume particles. While fume extraction in out-of-position welding can be more challenging due to the natural rise of fumes, proper technique and positioning can help maximize effectiveness. The Clean Air E™ fume extraction gun operates similarly to a standard MIG gun, making it easy for welding operators to adapt to. To achieve the best results, consider these best practices: By integrating the Bernard® Clean Air™ E fume extraction gun into your welding operations, you can enhance fume control while maintaining welding quality and efficiency. Fume extraction guns operate by capturing the fume generated by the welding process right at the source, over and around the weld pool. As with any piece of welding equipment, fume extraction guns benefit from preventive maintenance. Flux-cored wire allows vacuum adjustment Because flux-cored wire produces a slag, it generates more weld fume. However, one benefit of using self-shielded flux-cored wire, for example, is it allows the ability to increase the vacuum level of the gun. Welding operators can close off all the vents and utilize the long shroud. This action maximizes the vacuum at the front end of the gun without concern for disturbing the shielding gas, since there is none generates with self-shielded flux-cored wire. When using gas-shielded flux-cored wire, a 0 to 15-degree angle will help maximize fume collection. Pause at the end At the end of the weld, welding operators can pause for 10 to 15 seconds, holding the fume extraction gun in place without depositing weld metal. This action allows the gun to capture residual fumes as the weld bead is cooling. Wire type determines stickout The contact tip to work distance can be longer — about 1/2 inch to 3/4 inch — when welding with flux-cored wire and a fume extraction gun. With solid wire, welding operators should try to keep the stickout to 1/2 inch or less to maximize fume capture. These lengths are comparable to the stickout lengths used with standard MIG guns. Experiment with the air control regulator Some guns, like the Clean Air E™, incorporate a slider or toggle mechanism conveniently located on the gun handle, while others integrate this function internally. This adjustability is essential for balancing fume extraction with shielding gas coverage. Too much suction can disrupt the protective gas flow, leading to weld defects like porosity, while too little may not effectively capture harmful fumes. By using the built-in adjustment feature, operators can increase or decrease suction as needed to maintain optimal fume control while ensuring proper weld protection. Finding the right balance may require some trial and error. To optimize performance, welding operators should test the air control setting on scrap material before welding on a final product. This ensures that fume extraction is maximized without negatively affecting weld quality. With the Clean Air E™ and other adjustable fume extraction guns, operators have greater control over their work environment—helping to improve air quality while maintaining welding efficiency. As with any piece of welding equipment, fume extraction guns benefit from preventive maintenance. Caring for them is similar to caring for a standard MIG gun. Also note that using flux-cored wire with these guns requires more frequent gun maintenance than solid wire because of the slag and fumes it generates. Regular maintenance is important to help prevent a clog or spatter buildup, which can limit the fume capture rate. Inspecting and maintaining the front end of the gun is key to optimizing fume extraction. Frequently inspect the nozzle and contact tip for signs of spatter buildup, which along with blocking the fume extraction can also obstruct shielding gas flow and cause weld defects. Spatter buildup also can cause consumables to fail prematurely. Replace the consumables if spatter buildup appears, or clean them according to the manufacturer’s recommendations. Also, inspect the vacuum hose regularly for damage such as cuts or kinks, which can lead to loss of suction. Replace a damaged vacuum hose as necessary. Regarding consumables, using the manufacturer’s recommended consumables package with a fume extraction gun helps optimize performance, as the guns are engineered to get the best results with specific consumables. When in doubt about maintenance or any other aspect of using a fume extraction gun, consider working with a trusted welding distributor, certified industrial hygienist and/or the gun manufacturer to address any questions or concerns. In combination with many other variables in the welding operation — wire selection, specific transfer methods and welding processes, welding operator technique, and base material selection — fume extraction guns can help companies maintain compliance with safety regulations and create a cleaner, more comfortable welding environment. Proper use and maintenance of the equipment is important to get optimal results.
New industry standards from the Occupational Safety and Health Administration (OSHA) are protecting employees against potential health hazards in the workplace. These regulations, which dictate allowable exposure limits of welding fumes and other particulates (including hexavalent chromium), have led many companies to invest in fume extraction equipment. An increased desire to maintain optimal welding operator safety and to attract new skilled welding operators to the field is also a consideration in investing in this equipment — companies want to create the most comfortable and healthy work environment possible. The Clean Air E™ MIG fume extraction gun, as shown here, operates by capturing the fume generated by the welding process right at the source, over and around the weld pool. With interchangeable shroud options to help customize your extraction for your application. Some companies may opt for centralized fume extraction systems, which are designed to protect the entire shop area. These systems involve the installation of new ductwork and can be a costly investment for capturing fume particulate in the air. Fume extraction guns are available in a variety of amperages, cable styles and handle designs. As with any welding equipment, they have their advantages and limitations, best applications, maintenance requirements and more. In combination with many other variables in the welding operation; welding wire selection, specific transfer methods and welding processes, welding operator behavior and base material selection — fume extraction guns can help companies maintain compliance with safety regulations and create a cleaner, more comfortable welding environment. Fume extraction guns operate by capturing the fume generated by the welding process right at the source, over and around the weld pool. Various manufacturers have proprietary means of constructing guns to conduct this action, but at a basic level they all operate similarly: by mass flow, or the movement of material. This movement occurs by way of a vacuum chamber that suctions the fumes through the handle of the gun, into the gun’s hose through to a port on the filtration system (sometimes informally referred to as a vacuum box) like the Miller FILTAIR® 215 High-Vacuum Fume Extractor. The welding fumes that these guns remove are composed of a combination of the filler metal and base material. Some fume extraction guns feature adjustable extraction control regulators at the front of the gun handle, which allow welding operators to increase suction as needed (without affecting shielding gas coverage), while others provide this function internally. Regardless of the manner, the ability to balance between the downward flow of shielding gas and the upward flow of the suctioned air is critical. The fume extraction gun needs to provide the appropriate amount of shielding gas to protect the weld from defects such as porosity, without sacrificing the ability to suction fumes efficiently enough to protect the welding operator. The balance allows the weld pool time to react and solidify, and gives the fume particles time to decelerate so they are easier to extract. Typically, fume extraction guns are larger than regular welding guns and tend to be bulky due to the vacuum and hose necessary to extract the fumes. For that reason, some manufacturers create fume extraction guns with a vacuum hose swivel on the rear of the handle to make them easier to maneuver. Manufacturers have also, since fume extraction guns were first introduced (in the late 1960s and early 1970s), found ways to engineer internal components to minimize the handle weight in order to reduce operator fatigue. Fume extraction guns are well-suited for applications using solid welding wire and those in confined spaces. These include, but are not limited to applications in the shipbuilding and heavy equipment manufacturing industries, as well as general manufacturing and fabrication. They are also ideal for welding on stainless steel applications, as this material generates greater levels of hexavalent chromium, and on mild and carbon steel applications. The guns also work well on high amperage and high deposition rate applications and are available, typically, in 300 to 600 amp ranges. Fume extraction guns attach to a localized filtration system, as shown here. Fume removal occurs by way of a vacuum chamber in the fume extraction gun that suctions the fumes through the handle of the gun, into the gun’s hose through to a port on the filtration system. For the best results, fume extraction guns should be used for in-position welding, such as on flat butt welds. In this position, they can most effectively capture fume particles as they rise from the weld pool. In out-of-position welds, the energy of the fume particles causes them to rise at a high rate, making it more difficult for the fume extraction gun to draw them downward and through the vacuum hose. One distinct advantage to fume extraction guns is that they remove the fumes at the source. This will minimize the amount that enters the welding operator’s immediate breathing zone. As with any piece of welding equipment, fume extraction guns benefit from preventive maintenance. Caring for them is similar to caring for a standard GMAW gun. Regularly check for tight connections throughout the length of the fume extraction gun to ensure good electrical flow. Minimizing electrical resistance helps ensure consistent weld quality and prevent premature failure of the front-end consumables — contact tip, nozzle and diffuser. Frequently inspect the nozzle and contact tip for signs of spatter build-up, too, as such build-up can obstruct shielding gas flow and cause weld defects that ultimately will need to be reworked. Spatter build-up can also cause consumables to fail prematurely. Replace the consumables if spatter build-up appears or clean them according to the manufacturer’s recommendation. In some cases the shroud that surrounds the nozzle may also have to be replaced or cleaned free of spatter. To ensure optimal fume extraction capabilities, inspect the vacuum hose regularly for damage, including cuts or kinks that could lead to loss of suction. Replace a damaged vacuum hose as necessary and dispose of it according to the manufacturer’s and/or an industrial hygienist’s directions. Visually inspect the handle for cracks or missing screws, and also check that the gun’s trigger is not sticking or otherwise malfunctioning. Replace or repair these components as necessary. Finally, maintenance on the liner is also important. As with the vacuum hose, use compressed air to clear out any potential blockages during welding wire changeovers or when removing the wire from the gun. Spending an extra few minutes clearing out any debris from the liner can save considerably more time than troubleshooting the weld defects and equipment problems that can result from blockages. Also, track the amount of time that it takes for a liner to wear during the course of the welding operation. Replace the liner prior to that in the future to prevent downtime for replacement during shifts or problems with wire feeding or quality. When in doubt about maintenance or any other aspect of using a fume extraction gun, consider working with a trusted welding distributor, certified industrial hygienist and/or the fume extraction gun manufacturer to address any questions or concerns. Proper use of this equipment can help provide optimal results, and improve the safety and comfort of the welding environment. Regardless of your experience level, keeping your weld environment safe is a top priority. A multifaceted approach to fume mitigation can help you maximize safety and efficiency. Could it be time to take a closer look at your fume control strategies? Read our article published in the February issue of Fabricating & Metalworking. For the past 40 years, 4-Star Trailers in Oklahoma has built high-quality aluminum stock and horse trailers. Aluminum is lightweight, corrosion-resistant, and strong—ideal for trailers designed to endure tough road conditions. However, welding aluminum with a push-pull gun has its challenges. The heaviness of the tool can make it difficult to maneuver in tight angles, and the added weight can lead to welder fatigue, especially when working on large parts or frames. Additionally, this setup can cause delays in production timelines due to discomfort and inefficiency during long hours of use. Before switching to the Bernard® BTB Semi-Automatic Air-Cooled MIG Gun, the team regularly faced feeding issues. The feeding problems were especially noticeable when working on large aluminum parts, causing disruptions and affecting their ability to keep up with demanding production schedules. The difficulty in maneuvering the push-pull gun, coupled with the physical strain it placed on welders, contributed to frequent delays and a slower pace of work. The BTB Gun has been a game-changer. It pushes aluminum wire long distances with ease, something that wasn’t possible with the previous system. Its design is lightweight and maneuverable, making it far easier for welders to handle, especially in tight spots. This has significantly reduced fatigue, allowing the team to work longer and more comfortably without sacrificing quality. The customizable neck lengths of the BTB Gun are another huge advantage, allowing welders to reach into tight angles or handle bigger components with greater ease. The Easy Feed Liner in the BTB Gun reduces friction, making it simpler to feed aluminum wire and minimizing downtime—critical for maintaining a steady workflow in a busy shop. With fewer interruptions, the team is able to stick to production goals and meet deadlines more effectively. The use of AccuLock consumables also contributes to less maintenance, as they last longer than other options, cutting down on the frequency of replacements and the time spent on maintenance tasks. The biggest benefit? The team is more productive and satisfied with their work. With fewer interruptions and smoother operations, they’re able to produce high-quality welds faster. The BTB Gun has not only made their jobs easier but also helped the business run more efficiently. It’s become an indispensable tool in their shop, enabling them to build even tougher, more dependable trailers while improving overall productivity and welder satisfaction. MIG welding is a common welding process especially useful for beginner and DIY welders due to its easy-to-learn nature, shorter lead times and lower production costs. The versatility of MIG welding allows users to work on a wide range of materials with less stopping and restarting. The process features a continuous consumable wire electrode being fed through a welding gun and into a weld pool. The gun also feeds a shielding gas alongside the wire to protect the weld pool from contaminants. While there are different types of MIG guns that have unique parts (e.g., water-cooled, air-cooled, fume extraction), all MIG guns have some parts in common. Understanding the components of a MIG gun and the process by which it works will help you make decisions on the consumables and gun type you select for your job. Here’s what you need to know. 1. Nozzle 2. Contact Tip 3. Diffuser 4. Liner 5. Neck 6. Handle and Trigger 7. Cable Assembly 8. Insulator 9. Power Pin We’re thrilled to announce that Bernard® and Tregaskiss® have undergone an exciting brand refresh. As of today, you will notice our updated logos and visual branding on our website, social media channels, and promotional items. This change marks a significant step forward in our journey to enhance our brands’ presence and commitment to excellence in the welding industry. In a competitive market, it’s essential to evolve and stay ahead. Our refreshed visual identity reflects our We’re confident that these updates will strengthen our brands and provide you with an even better Mastering preventive maintenance, timely consumable replacements, and proper liner trimming are key to prolonging the lifetime of MIG welding equipment. Discover proactive measures to follow for enhancing durability and performance while decreasing downtime, boosting productivity, and cutting operating costs by reading our full article in the March 2024 issue of MetalForming Magazine. MIG welding is considered one of the easiest welding processes to learn and is useful for a variety of applications and industries. To maximize the benefits this versatile process offers, it is imperative to select the right MIG gun for the job. Choosing the right MIG gun directly affects efficiency, quality and safety — a trifecta every operator is trying to master to create a more comfortable and effective environment. There are five key factors when choosing the right MIG gun for your needs. More and more welding operations are investing in robotic welding systems to gain a competitive edge. Such systems not only deliver fine-tuned programming to ensure the accuracy, speed and repeatability needed for generating high-quality welds, they also further productivity and efficiency for an operation. Along with the productivity gains and quality improvements, saving money is a key reason companies are choosing to implement them. Here are seven ways companies can increase cost savings and ROI — beyond the benefits of the robotic welding system itself. Regardless of your skill level, you need to make sure that the equipment you use, works as hard as you do. Consider these components of your welding system to help weld conistency. Could it be time to take a good look at your equipment? Read our article published in the November issue of Fabricating & Metalworking. Learn how to recognize the key nuances between two welding-automation options, robots and cobots and how knowing these differences are essential to attain positive results. Have you ever wondered about the differences between robots and cobots? Learn more! “Choosing Between Robots and Cobots for Robotic Welding” in Metalforming Magazine South Louisiana Community College (SLCC) has made a game-changing decision to enhance its welding education program by incorporating Bernard semi-automatic welding guns and AccuLock consumables into its classrooms. This shift marks a significant departure from the MIG guns and consumables they had been using for decades. The transition began within the last year after SLCC’s welding technology instructors began noticing some challenges the students were facing with the welding guns and consumables that they were using. They noticed it took students 20 minutes to change a liner with their current welding guns and consumables. Enter Bernard. After meeting with the instructors and listening to their pains points and need for improvement – Bernard configured a lightweight MIG welding gun with the AccuLock S dual-locked liner consumable system to test in the classrooms. Instructors and students immediately saw the benefits. The AccuLock S dual-locked liner system makes liner installation error-proof by eliminating the guesswork and potential errors that can occur when trimming a liner. More importantly, it maximized their limited time in the classroom. The superior performance of AccuLock contact tips stood out most. SLCC saw a remarkable 50% improvement in tip life compared to the products they were using previously. AccuLock contact tips lasted twice as long. The school found the benefits of using Bernard’s MIG welding guns and AccuLock S consumables for instructional purposes were clearly evident. The lightweight and durable design, coupled with the extended consumable life delivered a substantial return on investment. Not only does the switch to Bernard provide cost savings, but it also equips inexperienced welders with the tools that can withstand the rigors of training and real-world applications. Estimated reading time: 7 minutes Speed, accuracy, repeatability — welding automation boasts some big benefits. Using robots across a myriad of manufacturing applications has been a boon to the welding industry, but it hasn’t come without its fair share of misconceptions. Accepting those misconceptions could actually negate those big benefits — and no one has the time (or money) for that. Here are some common myths heard ’round the manufacturing floor — and where we land on them. There seems to be a halo effect around the word “anti” — if it’s anti-“something,” it’s often assumed that the more you use, the better off you’ll be. In welding, that’s not necessarily the case. Using too much anti-spatter spray can actually cause more problems than it solves. When applying it to hot consumables, spraying just enough for it to dry on contact will create a sacrificial barrier that spatter won’t stick to as easily. If the solution is applied to the point where it’s dripping from the torch, it’s too much — and the excess spray will leak all over the parts and weld cell, leading to compromised weld quality, a messier weld cell and premature failure of the torch parts/consumables. Some operators will “dip” the consumables into a cup of the anti-spatter instead of spraying it, but this is also problematic because excess solution can cause the nozzle to become saturated and fail prematurely. When welds are off location, there’s usually an underlying issue that’s causing the problem. Tip bore wear, variations in stamping batches or parts being misaligned due to tooling/spatter can all create a situation where welds are off location. Here, reassessing TCP can help determine what the root problem is rather than just blaming the torch and touching up points. Apply only enough to get the job done. Tips to keep in mind when applying anti-spatter solution include: Contact tips can be the difference-maker between running an efficient welding process and accruing unwanted downtime. For smaller wire sizes in semi-automatic (or handheld) welding, using a contact tip that matches the size of the wire often leads to the desired results. However, in larger industrial operations where robotic welding is common, wire package size (vs. wire size) becomes more of the determining factor for selecting the proper tip size. Large-scale operations often use 1,000–2,000-pound drums or spools as the go-to options due to their high-volume output needs. The connection between the wire and the contact tip needs to be optimized for the tip to last as long as possible, which may require deviating from matching the tip and wire size. The adage goes, “You get what you pay for,” and that sentiment can definitely impact the quality of the work in welding. Investing in robotic welding equipment can add up quickly, so if there’s an opportunity to save a few bucks along the way, selecting a cheaper alternative seems like an appealing option. However, those savings often come at the expense of sacrificing product performance and weld quality, while creating more downtime. The issues experienced during the welding process will show in the end result, along with the bottom-line burn of frequent (and costly) consumable changeovers and excessive downtime for troubleshooting issues. Selecting high-quality, long-lasting consumables over cheaper alternatives will help reduce overall operating costs in the long run because it increases throughput while reducing inventory and downtime. Well … not necessarily. If the contact tip fails and you replace it, you can consider the problem “solved” for at least a short time. However, if the tip keeps failing quickly, it’s safe to say that there’s a greater issue at play. Many factors can cause a tip to fail, including feeding or grounding issues. In those cases, if you put a new tip on, you’re inevitably just waiting until it fails again because you’re not addressing the root cause. If you’re going through tips at a high rate, this is the time to assess your operation and make sure that the drive roll tension is correct and/or the liner is trimmed properly. These are two common issues that can easily cause excessive “burn backs”/tip failure. Choosing the right drive roll style and size for the wire being used is key to smooth and consistent wire feeding. However, if the tension is too high, or too low, it can diminish productivity, quality and efficiency. Tension that’s too tight can deform the wire, resulting in arc instability or burn backs (and too little tension can cause the wire to slip). If the system constantly needs more tension to push wire through, it likely means something else within the system is failing. For example, debris buildup in the liner can inhibit the right tension setting from being effective. To help mitigate the need to crank up the tension, make sure it is set correctly each time the wire spool/drum is changed. Additionally, be sure that the inlet guides are clear/not worn and clean the drive roll surfaces with a wire brush periodically to help maintain proper wire feeding. This is another instance where the idea of “more is better” can be misleading. You definitely need enough gas to cover the weld pool, but turning up the gas doesn’t necessarily result in less porosity — in fact, it could create turbulence and MORE porosity. Proper gas coverage is based on flow, not pressure. If a system isn’t set up properly and the nozzle gets blocked with too much spatter/debris, there won’t be sufficient gas volume (flow) to protect the pool. Leaks in the gas system or excess air flow within the weld cell can also impact the coverage of the weld pool, regardless of how high the gas flow rate is set. Instead of just defaulting to increasing the flow, do a quick run-through of the robotic system to verify that there is a proper tip-to-work distance and that the rest of the system is configured and running correctly. In many applications, weld locations are extremely important. Even though the robot is physically going where it’s programmed to go, if the wire isn’t placed in the joint properly, it could be detrimental to the end product. When welds are off location, there’s usually an underlying issue that’s causing the problem. Tip bore wear, variations in stamping batches or parts being misaligned due to tooling/spatter can all create a situation where welds are off location. Here, reassessing TCP can help determine what the root problem is rather than just blaming the torch and touching up points. Avoiding these common missteps in robotic welding will help you maximize uptime and throughput while minimizing costs — a win from start to finish. Written by Ryan Lizotte (ryan.lizotte@tregaskiss.com), Technical Services Manager, Tregaskiss. Estimated reading time: 5 minutes Self-shielded flux-cored welding is frequently used for structural construction and other jobsite welding since it offers a significant productivity advantage compared to stick welding. Welders using this process are likely holding their welding guns for much of the day, and they may be standing on elevated girders or lifts trying to get into tight places to complete a weld. Because of this, it’s important to choose a self-shielded flux-cored gun that is comfortable, lightweight and maneuverable to help get work done efficiently. Here are several key factors to consider when selecting a self-shielded flux-cored welding gun and tips for properly maintaining it to optimize performance. Not every welding gun fits every application. They come in various amperages and configurations, with features that include heat shields, configurable necks and adjustable cable lengths. The key is finding a flux-cored gun that works for each welder, since many options come down to operator preference. Guns rated at 350 or 450 amps are common in structural field welding applications. Guns rated at 600 amps are also available but used less often due to being heavier. It’s important to avoid undersizing the welding gun since it can lead to overheating and other problems. When selecting the gun amperage, consider the wire sizes that will be used most often. Typical wire sizes for a 350-amp gun are 1/16 inch and smaller. Wire sizes for 450-amp guns are 0.72 inch and larger, including 5/64 and 3/32 inch. Some self-shielded flux-cored guns are available with either a replaceable cable liner or a fixed cable liner. The demanding environments where self-shielded flux-cored welding takes place can be hard on the gun and consumables, so replaceable liners provide benefits. They offer quick and easy cable maintenance and can extend product life, since welders can change out components that have high levels of wear. Guns with replaceable liners also tend to have a lighter weight cable and provide more flexibility to weld around edges or corners. Guns with fixed cable liners are often larger, which can be an issue when welding in tight spaces. The cables are also typically stiffer and more rigid, so they can take more abuse. Once a fixed cable liner has reached the end of its useful life, the entire gun must be replaced. Gun necks are available in varying lengths and bend angles. The choice for the application often comes down to operator preference or weld joint access and configuration. A slimmer neck provides a better view of the weld pool and improved access to tight areas. A shorter neck typically provides more control compared to a longer neck. Still, operators may prefer a longer neck to increase the distance between themselves and the heat of the weld puddle — especially in higher amperage applications. Keep in mind that lightweight, rotatable necks help reduce operator fatigue by aiding with posture and positioning, and they improve weld visibility. In the field, triggers that get wet or covered in dirt still need to work, so it’s important to purchase a quality gun that includes a durable trigger. Look for a gun with an enclosed trigger. This protects the contacts inside a housing, so the trigger is less prone to wear and breakage. If you’re using a replaceable cable liner, it may have an internal or external trigger lead. Be aware that external trigger leads may require more maintenance because they can easily get snagged or catch on things like bolt heads. However, they are typically quick and easy to replace. A handle needs to be rugged and durable for the jobsite, but it should also feel comfortable in the operator’s hand. A self-shielded flux-cored gun with an optional dual schedule switch allows for wire speed adjustment while welding. In some guns, this switch is integrated into the handle to keep it protected from spatter. The ability to toggle between weld parameters easily—without having to stop welding and change settings—saves time and improves productivity. Beyond choosing the right gun for the job, it’s also important to use and maintain it properly. Consider these tips for optimizing gun performance. Store and handle it properly: Jobsites can be dusty, dirty places. Be sure to store guns and cables properly when not in use. Roll the cables up and put the gun away in a clean, dry place so there’s less risk it will be damaged. Maintain it as needed: Keep the gun and all components clean and check all connections periodically. Loose connections can cause electrical resistance and heat buildup, which can result in premature wear. Take the time to regularly blow out the liner with clean, compressed air to remove dirt and debris. Immediately address any damage to the gun components with maintenance or replacement. Invest in quality consumables: Consumable choice often comes down to cost or operator preference. However, investing in high-quality consumables can help extend the life of the gun, provide better performance and reduce downtime for changeover. The self-shielded flux-cored process can deliver significant benefits for productivity and efficiency. Choosing the right gun and components—and maintaining them properly—plays a key role in optimizing your results. Written by Stephen Bennett (stephen.bennett@bernardwelds.com), Mechanical Engineer, Bernard, Republished with permission from Modern Contractor Solutions (August, 2023) Tregaskiss and Bernard, manufacturer of semi-automatic, fixed automatic, cobot and robotic MIG welding guns, consumables and peripherals exhibited at FABTECH 2023, September 11-14 in Chicago. FABTECH is North America’s largest metal forming, fabricating, welding and finishing event that brings over 1,500 world-class suppliers worldwide together in one place. This year Bernard and Tregaskiss presented its latest technology and cost-effective welding solutions to help manufacturers and fabricators improve weld quality and productivity. This year’s product showcase included: Additional options include nozzle detect and wire cutter, and installed on the TOUGH GUN® reamer stand. , plus all TOUGH GUN TT4 reamer robotic nozzle cleaning stations come with an industry-leading 2 year warranty that can be extended to 3 years with exclusive use of TOUGH GARD anti-spatter liquid. Today, even the smallest weld shops are making the jump to robotics, and even the largest, highly automated OEMs likely have semiautomatic weld cells for repairs or for welding parts that don’t lend themselves to automation. In automotive manufacturing, these manual cells may be midway through the line for welding frames or at the end for minor rework. If you’re in heavy equipment manufacturing, you might automate multipass welding on thick parts and reserve semiautomatic welding for tacking the parts or adding specialized components. No matter your industry or your level of welding automation, an effective weld cell layout can help. Work needs to flow in an orderly fashion. Power, grounding, and wire feed cables need to be properly managed. And, of course, you need to ensure welders can work safely, consistently, and with good ergonomics. Proper layout supports high productivity and quality, along with cost savings. Whether robotic or semiautomatic, a well-designed weld cell makes efficient use of available space, where every component—the power source, welding gun, weld table, cables—ensures parts can be produced with little interruption. Streamlining workflow is a good first step. This involves setting up equipment in a way that helps operators avoid handling parts multiple times. Double handling of parts adds non-value-added seconds to the overall manufacturing cycle time and reduces the capacity for completed parts sent out the door. Think with an assembly line mentality. Look beyond the weld cell to how parts are being delivered. For example, when an operation requires that parts receive semiautomatic tack welds before robotic welding, work must flow at a consistent pace to prevent the welding robot from sitting idle. To ensure a steady supply of parts and prevent bottlenecks, the cell should have a single point of entry. For optimal workflow, parts should move out of the weld cell in the same direction. Minimize the distance a part needs to travel by keeping assembly points close together. Weld cells contributing to the completion of a single weld assembly should be in the same area of the facility. This proximity not only reduces time for moving a part, but it also lessens the number of footsteps operators need to make. Excessive movement in a welding cell is considered non-value-added work. If you notice bottlenecks or operators or welding robots standing idle, or operators walking too far between weld cells, you might consider performing an audit. Any idle operation results in a failure to capitalize on the investment of that process. An audit can help you identify the causes behind these problems and implement solutions. The aim is to balance out the operations so that every aspect contributes to value-added work and high productivity. Welding ergonomics are at the center of a semiautomatic welding cell layout. A more comfortable, healthier welding operator is a more productive one. Setting up the weld cell in a way that minimizes the need to reach repetitively or move awkwardly can reduce the risk of work-related musculoskeletal disorders. Try to position the workbench or workpiece between the welding operator’s waist and shoulders, since this promotes a neutral posture that reduces stress on the body. When welding large components, use positioners or weld tables that move or rotate the part to the correct height and angle. The same holds true when providing operators with a MIG gun that suits them, whether it be a curved or straight handle. Locking triggers help support comfort, as do rubber mats to stand on. Strategically locating the power source and wire feeder can make the cell more efficient. Keep the two pieces of equipment as close as possible, so the operator can easily access them. Close proximity allows for shorter power cables for smoother wire feeding and also reduces electrical resistance drops so welding parameters remain more consistent. Keep ground cable connections to a minimum. Some companies string together welding cables between weld cells for the same power source. This practice is inefficient, however, and can lead to problems. The multiple junctions can wear out easily, which causes electrical resistance and poor weld quality over time. The electrical resistance also can shorten consumable life, resulting in erratic arcs and burnbacks, leading to more downtime for contact tip changeovers. Implementing an effective robotic welding cell layout requires careful planning and attention to detail. One of the best approaches is to test the layout through virtual modeling or 3D simulation. These software programs can simulate the welding gun configuration—neck length, nozzle, and mounting (solid versus clutch)—to ensure it will operate properly within the work envelope. They also consider weld sequencing, robot arm movement, fixturing, and the parts to be welded so that you can be confident everything will work as planned. Take the time to simulate the weld cell layout and process before equipment integration to avoid issues once the welding robot is in service. Simulations help prevent downtime during mass production for troubleshooting and potential expenses for revamping tooling or replacing components. They also can model another key factor—welding robot reach. Be sure to match the size of the part with the reach of the robot. The robot must be able to reach all weld joints on the part; otherwise, you might need multiple robots for the application. A single, small welding robot won’t suffice for welding on a large part. If you have a weld on the edge of the reach envelope, you might not be able to achieve the optimal welding gun angle to create quality welds. This can add costs for rework, and you’ll likely need to replace stretched power cables that fail prematurely. Regarding tooling, you might be tempted to purchase less expensive options—though such tooling might not have the features you need, such as the appropriate number of clamps or location pins. This can lead to inconsistent part fit-up or locating that requires multiple passes to fill the weld joint, adding to cycle time. You might experience more downtime as you reprogram the welding robot to accommodate the gaps, or you may end up needing to invest in touch sensing to locate the joint. Even worse, you might need to upgrade your tooling after the initial design phase—a costly step. Also consider the positioners. Their size and weight capacity must account for both the weight of the part and the tooling. Design the robotic cell for the heaviest part to be welded. Where you place the power source and wire feeder matters as they both impact power cable management and grounding. If space is at a premium, you may want to place the welding power source above the robot cell on a mezzanine. This way, you can run the power cable and ground leads down channels in the cell’s back wall directly to the tooling and welding robot. These leads are stationary—except for the ones on the robot, so be sure to account for the robot’s air movements to minimize wear on the cables. Placing a junction power block at the base of the robot and running a high-flex power cable from that base up to the wire feeder can help save time in repairs, and it can save money. If the high-flex cable becomes worn, you just replace that shorter piece instead of the entire cable. The same approach works for the grounding leads. Finally, determine the best location for the nozzle cleaning station or reamer. This peripheral cleans the nozzle of spatter during routine pauses in welding. It helps extend consumable life and reduces downtime for changeover. The reamer needs to be close enough for the robotic welding gun to engage fully for the ream cycle. If you’re operating two robots close together, you can program them both to use the same reamer. Avoid mounting the reamer anywhere but a flat surface, since positioning it at an angle can cause anti-spatter to leak over equipment or fixtures. Avoid interrupting the weld cycle by cleaning the nozzle during robot idle time. For example, consider cleaning the nozzles while parts are being transferred in and out of the fixture or while components are being loaded into a weld cell. If you’re experiencing bottlenecks or missing productivity or quality goals, take a look at the welding cell layout. In a semiautomatic setup, never overlook welder comfort and safety. In a robot cell, moving power cables, power sources, wire feeders, or anything else can change how much that cell can produce over a shift. The little things matter, and missing just one detail can snowball into bigger problems down the road. Small changes can make a big impact on the efficiency you can achieve. Written by Justin Craft (justin.craft@bernardwelds.com), Field Technical Services Specialist, Tregaskiss and Bernard, Republished with permission from The Fabricator (August, 2023). Estimated reading time: 6 minutes The welding gun is a vital piece of equipment in a robotic welding system, serving as the conduit for the welding wire, gas, and power. However, it can sometimes be an afterthought when companies implement an automated welding solution. Unfortunately, this oversight can lead to a host of problems, not to mention frustration. That is especially true for first-time users making the investment. The wrong robotic welding gun can also cause issues for those more experienced with robotic systems. It’s not uncommon for companies to purchase the same gun for a new robot and tooling when, in fact, it may not be the best option. Companies also need to determine their welding amperage and arc-on requirements for the application. This ensures that they purchase a robotic welding gun with the proper duty cycle — the amount of welding that can occur at a rated output over a period without causing damage to the gun. Robotic welding guns are available in a variety of ratings, including air-cooled models that operate at 350 or 385 A at 100% duty cycle. Today, most robotic welding systems are through-arm models in which the power cable runs through the casting of the robot arm. As a first step in configuring a robotic welding gun for these systems, it’s important to know the make and model of the robot, power source, and wire feeder. Each equipment manufacturer has a different interface that dictates how each piece of equipment connects with one another. There are higher amperage water-cooled options, which are typically 400 A and above, available in the marketplace. Some of these may be rated at 100% duty cycle, while others are rated at 60%. Don’t be fooled by high amperage unless it’s at 100% duty cycle. Hybrid options are available for companies that want the simpler construction of an air-cooled robotic welding gun with the added cooling capacity of a water-cooled one. These guns have external water lines that circulate water around the nozzle to keep the front-end consumables cooler. For a robotic welding gun to access the weld joints, it’s critical that the work envelope is adequate. Companies need to consider not just the size of the gun but also the space that is available when the tooling, fixtures, and parts are all in place. Joint design and weld sequencing also factor into the equation. It’s important that there is room and time for the welding gun to weld the joints in a sequence that keeps heat to a minimum. Companies should avoid heat soaking the parts, so they don’t become distorted. A robot integrator can conduct a 3D simulation using models provided by the robotic welding gun manufacturer through computer-aided design (CAD) to make sure the gun and neck have the proper access and reach within the given space. The CAD model can also show whether the selected gun has the correct tool center point (TCP) and can extend to the nozzle cleaning station for reaming or to a service window for consumable changeover. A service window supports safety in the operation by eliminating the need for an employee to physically enter the cell. Some robotic welding gun manufacturers offer online configurators that allow companies to customize the equipment for their exact application. These configurators guide the user through a step-by-step process, providing options to choose from for each component. With or without this tool, companies need to consider what their needs are based on their upfront assessment. Gun mount: There are two mounting options for a robotic welding gun to protect it in the event of a collision — a solid arm mount and a clutch. If the robot or end user’s safety procedure requires external collision detection, a clutch can be added to the system. This component functions both mechanically and electrically by recognizing a collision and sending a message to the robot controller to stop the system. If procedures allow for reliance on only the robot’s collision detection, then a solid mount will suffice. Neck: The neck length and angle must provide the approach angle to weld parts properly and to allow for smooth wire feeding. Standard neck angles are 22, 45, and 180 deg. Through-arm robots generally use a 45-deg neck; however, that should be verified with the CAD model/simulation before implementing. Companies will also need to take into consideration the welding wire they are using. For example, aluminum wire requires a straighter neck to feed through properly since it is so soft. Welding cable: For through-arm robots, the make and model dictate the cable length. For conventional robots (where the cable assembly runs outside the robot arm), the gun cable length also depends on the robot make and model along with the location of the feeder. It may be remotely mounted or mounted on the robot itself. There is more flexibility with cable length for these robots, but it’s important not to use too long of a cable since this can lead to wire-feeding issues. Conversely, a cable that is too short can stretch and break down quickly. Welding consumables: When choosing contact tips for the robotic welding gun, look at the welding process. Pulsed gas metal arc welding (GMAW-P), for example, is quite hard on contact tips due to its high-frequency waveforms. This process requires a harder tip or a contact tip specifically designed for pulsed welding. The chosen nozzle needs to allow proper access to the weld joint. A tapered nozzle works well when using smaller-diameter wire and contact tips. Higher-premium consumables are a good choice since these last longer and reduce downtime and labor for changeover. Welding supervisors and operators should schedule time to perform preventive maintenance, such as checking connections and visually inspecting consumables for spatter, during routine pauses in welding. Liners are another factor to consider, and the welding wire being used affects the choice. Flux- and metal-cored wires tend to be stiffer and harder to feed than solid wires. They require an extra-heavy-duty liner to support the wire and gain smooth feedability as it moves toward the contact tip. A D-wound galvanized wire works well. Companies can also use this liner for solid wire with good success. Companies invest in robotic welding systems to increase quality, productivity, and cost savings through a fast, repeatable process. To gain those benefits, every part of the system needs to be functioning optimally. Ensuring that the robotic welding gun has been configured properly before implementing the system can prevent downtime and extra expenses. This article was written by Ryan Lizotte (project manager, Tregaskiss, Windsor, Ontario, Canada) for the American Welding Society. Estimated reading time: 6 minutes While MIG is widely used, some operations may still run into issues that require troubleshooting. Understanding the basics of MIG welding and following best practices for operator technique as well as gas and consumable selection can help optimize results with the process. MIG offers productivity benefits when compared to some other welding processes such as TIG and Stick, thanks to its higher travel speeds and deposition rates. MIG is also considered easier for new welders to learn, so it can be a good option for operations that struggle to find skilled welders. MIG could be utilized with either solid filler wires or tubular wires such as Metal Cored and when used with Flux Cored wires it is referred to as Flux Cored welding. Tubular wires in general can be run at higher speeds and deposit more weld metal, so they even offer higher productivity gains than Solid wires. There are many factors to consider when choosing the right welding process for your application. These include base material type and thickness, weld appearance requirements, productivity requirements, the welding environment and available skilled labor. TIG welding is generally used in niche applications, such as those that require high-precision welds or extremely high aesthetic quality. TIG is frequently used with special-grade materials like titanium or stainless steel. In comparison, MIG can be used in higher production applications where increased throughput is important, and it’s a good option for a wide variety of metals. A typical travel speed in TIG welding is 4-6 inches per minute. With MIG welding, travel speeds are much higher; 6 inches per minute are considered slow, and 15 to 20 inches per minute are common. Deposition rates are also much higher with MIG welding. Regarding training, TIG is considered the most difficult welding process to learn and master since it uses both hands. An operator may take a few months to become proficient in TIG, while a new welder could be proficient in MIG within a week or two. Shielding gas plays an important role in determining weld penetration profiles, arc stability, mechanical properties of the finished weld, the transfer process you use and more. The filler metal manufacturer often provides shielding gas recommendations for the type of wire being used, so it’s a good idea to first consult the wire specification sheet. When using flux-cored wire, 100% CO2 or an 80/20 Argon/CO2 mix are common choices. When it comes to solid wire or metal-cored wire, the right gas is dependent on the transfer mode being used. A short-circuit transfer mode works with 100% CO2 gas in most cases but can still run on mixed gas. While using a pulse or spray transfer, a higher Argon content is needed, and an 80/20 Argon/CO2 is the right choice. The base material also plays a role in choosing the right gas. Aluminum requires 100% argon, while stainless steel requires at least 98% argon. The technique choice may come down to operator preference in most cases, but there are some best practices. For example, when welding aluminum, a push angle is generally better because it helps the cleaning action of the oxidation layer on aluminum, similarly uphill position, a push angle is good for visibility and penetration. While if you use Flux Cored wire to weld carbon steel then a pull angle is going to work better in this case to give enough time to the slag not to be entrapped in the weld metal. Maintaining a proper stick-out is important to achieving the best results in MIG welding, a too-long or a too-short stick-out will affect the weld quality and appearance. A 3/8-inch stick-out is a good starting point, but operators can deviate from that based on preference, wire diameter and accessibility to the weld. To choose the right MIG welding gun, consider the specifics of the application. The wire feed speed and wire diameter are two of the most important factors in determining proper gun amperage. Are you welding heavy wall materials, like heavy equipment or heavy steel structures? Those jobs will likely require a high deposition, hence a high-amperage welding gun — such as an Air-cooled 400-amp gun with at least a 60%-80% duty cycle or above, and in some cases a water-cooled gun. If you weld lighter walls and shorter beads, you may consider a 200 to 300-amp gun. The most common amperage choice in the industry is a 300- to 400-amp, air-cooled MIG gun. This gun can address the majority of the MIG welding applications and can run the most common wire sizes such as 0.045” and 0.052”. A good starting point would also be the welding procedure in place that specifies the amperage needed for the weld, which would help in choosing the gun’s amperage. Another easy way is to match the welding machine amperage output, a 400-amp welder would run well with a 400-amp gun in most cases, but this might not be the most effective way to select the right amperage gun when compared to the other methods mentioned above. Using the OEM consumables designed to be used with a specific MIG gun and welding system is important. Because these consumables are machined to very tight tolerances and go through high-quality measures which in turn is translated into higher quality welds and longer consumable life. Be sure to choose a contact tip that is the appropriate size for the wire diameter — an oversized or undersized contact tip will wear faster and result in poor performance. In addition, follow the gun manufacturer’s recommendations for consumable installation and changeover, check connections regularly, install and trim to the right length, select the right nozzle material, size and recess/extension, and finally clean your consumables regularly and change them when needed. Written by Mostafa Hanafy (mostafa.hanafy@tregaskiss.com) , Market Segment Manager, Tregaskiss and Bernard. Republished with permission from Fabricating and Metalworking (August 2023). Estimated reading time: 4 minutes While it may be tempting for companies to purchase MIG welding guns and welding consumables based on price, lower upfront costs don’t always add up to savings. Less expensive products often lack in quality and bring risk to the profitability of the welding operation. This can come in the form of: For these reasons, it’s important to look at MIG guns and consumables as more than simple commodities. Welding engineers, production managers and purchasing agents, along with other stakeholders, should instead look at the total cost of ownership of these products. Those with a higher upfront cost can help reduce risks and save money in the long term. When considering the total cost of ownership of a MIG gun, there are several factors to keep in mind. For example, less expensive guns may require more maintenance and repairs over the life span of the product. Parts like necks, handles and triggers may need frequent attention, resulting in increased expenses for replacement and downtime for changeover. With labor being the largest expense in a welding operation, time spent on activities other than welding come at a price. Lower quality guns may also require more downtime for troubleshooting issues like poor wire feeding. This not only stops production, preventing parts from moving out the door, but it also keeps welding supervisors or others from more important tasks. When an employee’s job is to keep the weld cells running smoothly, any distraction for troubleshooting can negatively affect the productivity and profitability of the welding operation. To lower the total cost of ownership of a MIG gun, companies should look for quality products with a long life span. Guns that offer the ability to repair the power cables are a good option. In this case, the downtime and cost for replacement is a benefit. It is less expensive to repair the cable than to buy a brand-new gun. Companies should also look at a gun’s warranty. With heavy industrial use, a high-quality MIG welding gun typically lasts one to two years and those, like Bernard® BTB guns, include a one-year warranty. Some Bernard guns also have a lifetime warranty on triggers, switches and handles. Poor quality, cheaper consumables — contact tips, gas diffusers, nozzles and liners — can lead to a host of problems that increase downtime and costs. These include an erratic arc, burnbacks, birdnests and a short life span (particularly for contact tips) that can lead to rework. Such issues also increase instances of troubleshooting and make less expensive consumables pricier in the long term. Cheaper contact tips can be prone to keyholing, or an uneven wear of the bore, and may not be as consistent in terms of electrical conductivity. Both can affect welding performance and shorten product life. Conversely, premium consumables can lower the total cost of ownership in a welding operation. The longer they last, and the easier they are to install, the less downtime for changeover and the less expense for replacement. AccuLock™ contact tips feature a coarse thread that eliminates cross-threading and 60% of this consumable is buried in the diffuser, so it is away from heat during welding. As a result, these contact tips last two to three times longer than competitive ones. For robotic applications, AccuLock HDP contact tips last six to 10 times longer. This extended life can help increase production by reducing the number of scheduled changeovers. QUICK LOAD™ liners are also a good option for robotic applications, as they load from the front of the robotic welding gun — safely out of the weld cell — in less than half the time needed for a conventional liner. The liner in the AccuLock S consumable system offers error-proof liner trimming without measuring, to prevent issues with wire feeding. When it comes to MIG guns and consumables, time is money. Repairs, replacements and rework all add up and affect the total cost of ownership of these products — not to mention the company’s bottom line. Making a conversion to higher quality options can yield good results and the benefits can be verified with a MIG gun and consumables trial prior to implementation. These trials help establish a baseline for improvements and provide data that allows companies to assess the upfront cost of products compared to the cost of downtime. With this information in hand, companies can make an informed decision about alternative MIG welding guns and consumables. The New Clean Air E™ Fume Extraction MIG Gun Offers Superior Fume Capture, Enhanced Ergonomics
The New Clean Air E™ Fume Extraction MIG Gun Offers Superior Fume Capture, Enhanced Ergonomics
Up to 95% fume capture efficiency and optimized design make workspaces safer and reduce welder strain
Attacking Weld Fume at the Source
Attacking Weld Fume at the Source
The basics
Benefits of the Bernard® Clean Air™ E Fume Extraction Gun
Maximizing Performance
Proper maintenance and consumable usage
Fume extraction guns can provide results
Learn more about the Bernard® Clean Air E™
Fume Extraction Guns: Understanding the Basics
Fume Extraction Guns: Understanding the Basics
The basics of fume extraction guns
Applications, advantages and limitations
Maintenance tips
The Importance of Implementing a Layered Approach to Fume Mitigation
The Importance of Implementing a Layered Approach to Fume Mitigation
Bernard® BTB Gun Transforms Aluminum Welding for 4-Star Trailers
Bernard® BTB Gun Transforms Aluminum Welding for 4-Star Trailers
Key MIG Gun Components for Job Performance
Key MIG Gun Components for Job Performance
CONSUMABLES
ESSENTIAL GUN COMPONENTS
OTHER COMPONENTS
A Fresh Look for Bernard® and Tregaskiss®
A Fresh Look for Bernard® and Tregaskiss®
What’s New?
Bernard and Tregaskiss, while maintaining the core values and heritage of our brands.
convenience, tregaskiss.com will continue to redirect to the new site.
millerweldsstore.com and we’ve begun to provide new marketing collateral to our sales team.
rolled out gradually as existing stock is replenished.What’s Staying the Same?
MIG welding solutions remains steadfast.
durability of Bernard and Tregaskiss products.
excellence in robotic MIG guns continue to be the foundation of our brands.Why the Change?
dedication to innovation and leadership in the welding industry. By creating a more cohesive and modern brand image, we are reinforcing Bernard’s reputation as a leader in semi-automatic MIG gun solutions and Tregaskiss’ prominence in robotic MIG guns.Impact on Products and Marketing Materials:
existing stock is replenished.
durability and toughness of our products.
experience. If you have any questions or need further information, please do not hesitate to contact us.Extending the Life of Welding Guns and Consumables
Extending the Life of Welding Guns and Consumables
5 Factors to Consider When Choosing a MIG Welding Gun
5 Factors to Consider When Choosing a MIG Welding Gun
Click here to read the full article featured in the March 2024 issue of Fabricating and Metalworking Magazine.Ways to Save More Money With a Robotic Welding System
Ways to Save More Money With a Robotic Welding System
Read the full article featured in Fabricating & Metalworking Magazine.Five Equipment Adjustments to Improve Weld Quality
Five Equipment Adjustments to Improve Weld Quality
Choosing Between Robots and Cobots for Robotic Welding
Choosing Between Robots and Cobots for Robotic Welding
South Louisiana Community College Chooses Bernard® Semi-Automatic MIG Welding Guns and AccuLock™ Consumables for Welding Education | Customer Testimonial
South Louisiana Community College Chooses Bernard® Semi-Automatic MIG Welding Guns and AccuLock™ Consumables for Welding Education
Understand the Truth About These 7 Robotic Welding Myths
Understand the Truth About These 7 Robotic Welding Myths
Myth 1: The more anti-spatter solution you use, the better the results
Myth 2: Using a contact tip that matches the size of the wire always leads to the best results
Myth 3: The cheapest products will work
Myth 4: Changing the contact tip will always solve the problem
Myth 5: Higher drive roll tension results in better wire feeding
Myth 6: Increased gas flow results in less porosity
Myth 7: Off-location welds are always the gun’s fault
Republished with permission from Fabricating and Metalworking, (October 2023)Self-Shielded Gun Performance
Self-Shielded Gun Performance
1. Flux-Cored Gun Options
2. Amperage
3. Replaceable or Fixed Cable Liners
4. Necks
5. Trigger
6. Handle
The Best Results
Closing Thoughts
Bernard® and Tregaskiss® offer welding solutions at FABTECH 2023
Bernard® and Tregaskiss® offer welding solutions at FABTECH 2023
Best Practices For Weld Cell Layout
Best Practices For Weld Cell Layout
The Big Picture
The Semi-Automatic Weld Cell
The Robotic Weld Cell Layout
Small Moves, Big Impact
Proper Robotic Welding Gun Configuration
Proper Robotic Welding Gun Configuration
Configuring the Gun
Maintaining Efficiency
MIG Welding FAQ: Best Practices for MIG Success
MIG Welding FAQ: Best Practices for MIG Success
MIG is the most frequently used welding process in general manufacturing and fabrication, thanks to its ease of use, versatility, and productivity benefits.
Q: What are the main advantages of MIG welding?
Q: What are the differences between MIG and TIG welding?
Q: What is the right shielding gas for MIG welding?
Q: Which is better: a push or a pull technique?
Q: What is the proper wire stick-out?
Q: What amperage MIG welding gun is needed?
Q: How can an operation make consumables last longer?
Upfront Cost vs. Total Cost of Ownership of MIG Guns and Consumables
Upfront Cost vs. Total Cost of Ownership of MIG Guns and Consumables
A look at MIG welding guns
Considerations for consumables
MIG gun and consumables trials