Attacking Weld Fume at the Source
The Occupational Safety and Health Administration (OSHA) and other safety regulatory bodies set the allowable exposure limits for weld fumes and other particulates, including hexavalent chromium, with the aim of protecting employees against potential health hazards in the workplace. Providing welding operators with proper ventilation during the welding process is an important step companies can take to help meet the standards — and to help provide a safe and comfortable work environment.

Companies may opt to invest in centralized fume extraction systems, which are designed to protect the entire shop area. These systems involve the installation of new ductwork and fans to remove fumes and are highly effective, but they are also more expensive than other options. A viable alternative for some companies is a fume extraction gun used in conjunction with a fume extraction device or localized filtration system.
Fume extraction guns are available in a variety of amperages (typically 300 to 600), cable styles and handle designs. As with any welding equipment, they have their best applications, advantages and limitations, as well as recommended techniques for achieving the best results.
The basics
Fume extraction guns operate by capturing the fume generated by the welding process right at the source, over and around the weld pool. The weld fumes removed by these guns are composed of a combination of the filler metal and base material.
Various manufacturers have proprietary means of constructing guns to conduct this action, but at a basic level they all operate similarly: by mass flow, or the movement of material. A vacuum chamber suctions the fumes through the handle of the gun, into the gun’s hose and through to a port on the filtration system (sometimes informally referred to as a vacuum box).

Typically, fume extraction guns are larger than regular welding guns, and include the vacuum and hose that are necessary to extract the fumes. Some manufacturers offer fume extraction guns with a vacuum hose swivel on the rear of the handle to make them easier to maneuver. Also, design advancements have minimized the handle weight and size to make the guns as light as possible for operator comfort, while still offering consistent fume extraction benefits.
Benefits of the Bernard® Clean Air™ E Fume Extraction Gun
The Bernard® Clean Air E™ fume extraction gun is designed to efficiently capture welding fumes at the source, helping to create a cleaner work environment. This gun is particularly well-suited for applications using solid welding wire and for operations in confined spaces, where fume extraction directly in the welding operator’s breathing zone is essential.
Industries that frequently benefit from this technology include shipbuilding, heavy equipment manufacturing, and general fabrication, especially when working with mild or carbon steel. Additionally, for applications in petrochemical industries or those involving stainless steel welding, where higher levels of hexavalent chromium are present, the Clean Air E™ gun provides an effective solution for improving air quality.
Designed for high-amperage and high-deposition rate applications, this gun performs best in flat and horizontal welding positions, where it can effectively capture rising fume particles. While fume extraction in out-of-position welding can be more challenging due to the natural rise of fumes, proper technique and positioning can help maximize effectiveness.
Maximizing Performance
The Clean Air E™ fume extraction gun operates similarly to a standard MIG gun, making it easy for welding operators to adapt to. To achieve the best results, consider these best practices:
- Optimize Extraction Settings – Adjust the vacuum system like the Miller FILTAIR® 215 to balance fume capture without affecting shielding gas coverage.
- Maintain Proper Gun Positioning – Keep the gun at the recommended angle to ensure optimal fume collection.
- Perform Regular Maintenance – Clean the extraction system and gun components to maintain consistent performance.
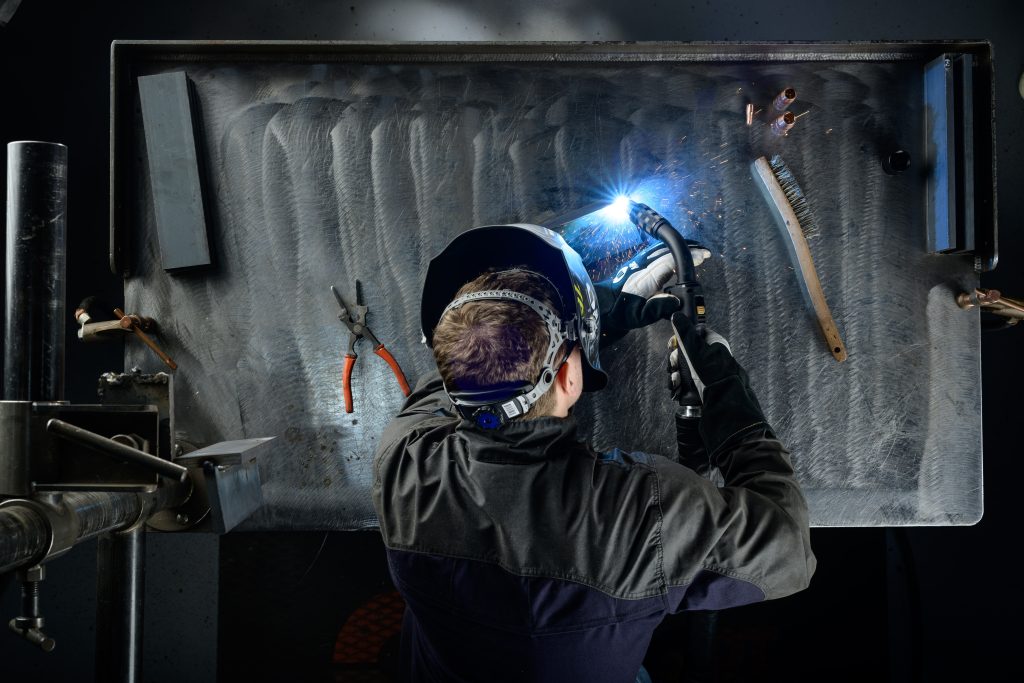
By integrating the Bernard® Clean Air™ E fume extraction gun into your welding operations, you can enhance fume control while maintaining welding quality and efficiency. Fume extraction guns operate by capturing the fume generated by the welding process right at the source, over and around the weld pool. As with any piece of welding equipment, fume extraction guns benefit from preventive maintenance.
Flux-cored wire allows vacuum adjustment
Because flux-cored wire produces a slag, it generates more weld fume. However, one benefit of using self-shielded flux-cored wire, for example, is it allows the ability to increase the vacuum level of the gun. Welding operators can close off all the vents and utilize the long shroud. This action maximizes the vacuum at the front end of the gun without concern for disturbing the shielding gas, since there is none generates with self-shielded flux-cored wire. When using gas-shielded flux-cored wire, a 0 to 15-degree angle will help maximize fume collection.
Pause at the end
At the end of the weld, welding operators can pause for 10 to 15 seconds, holding the fume extraction gun in place without depositing weld metal. This action allows the gun to capture residual fumes as the weld bead is cooling.
Wire type determines stickout
The contact tip to work distance can be longer — about 1/2 inch to 3/4 inch — when welding with flux-cored wire and a fume extraction gun. With solid wire, welding operators should try to keep the stickout to 1/2 inch or less to maximize fume capture. These lengths are comparable to the stickout lengths used with standard MIG guns.
Experiment with the air control regulator
Some guns, like the Clean Air E™, incorporate a slider or toggle mechanism conveniently located on the gun handle, while others integrate this function internally.
This adjustability is essential for balancing fume extraction with shielding gas coverage. Too much suction can disrupt the protective gas flow, leading to weld defects like porosity, while too little may not effectively capture harmful fumes. By using the built-in adjustment feature, operators can increase or decrease suction as needed to maintain optimal fume control while ensuring proper weld protection.
Finding the right balance may require some trial and error. To optimize performance, welding operators should test the air control setting on scrap material before welding on a final product. This ensures that fume extraction is maximized without negatively affecting weld quality.
With the Clean Air E™ and other adjustable fume extraction guns, operators have greater control over their work environment—helping to improve air quality while maintaining welding efficiency.
Proper maintenance and consumable usage
As with any piece of welding equipment, fume extraction guns benefit from preventive maintenance. Caring for them is similar to caring for a standard MIG gun. Also note that using flux-cored wire with these guns requires more frequent gun maintenance than solid wire because of the slag and fumes it generates. Regular maintenance is important to help prevent a clog or spatter buildup, which can limit the fume capture rate.
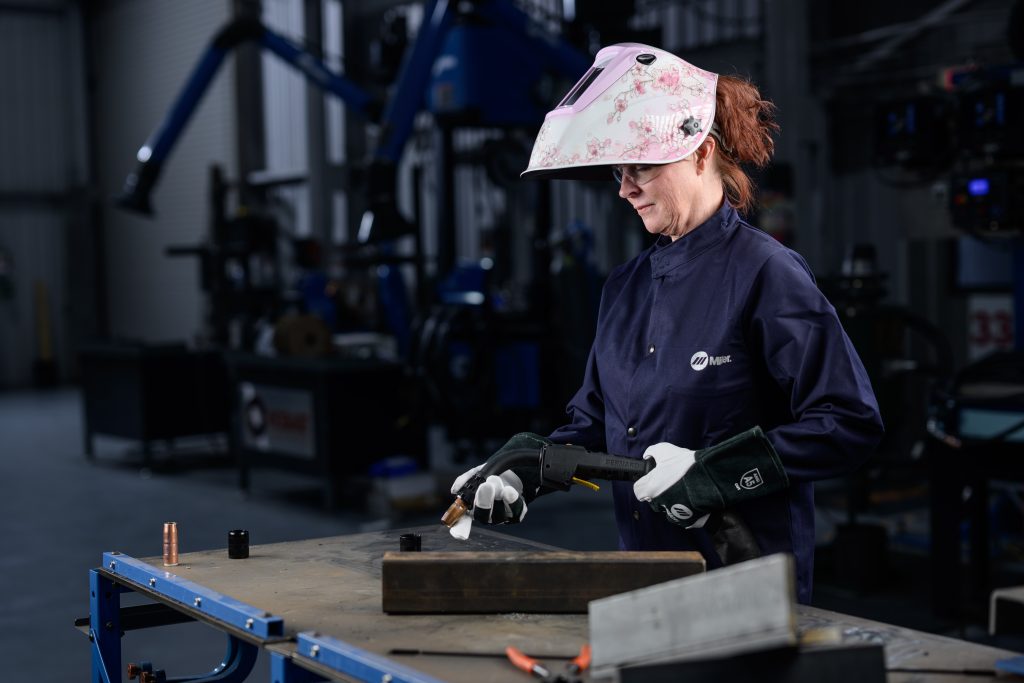
Inspecting and maintaining the front end of the gun is key to optimizing fume extraction. Frequently inspect the nozzle and contact tip for signs of spatter buildup, which along with blocking the fume extraction can also obstruct shielding gas flow and cause weld defects. Spatter buildup also can cause consumables to fail prematurely. Replace the consumables if spatter buildup appears, or clean them according to the manufacturer’s recommendations.
Also, inspect the vacuum hose regularly for damage such as cuts or kinks, which can lead to loss of suction. Replace a damaged vacuum hose as necessary.
Regarding consumables, using the manufacturer’s recommended consumables package with a fume extraction gun helps optimize performance, as the guns are engineered to get the best results with specific consumables.
When in doubt about maintenance or any other aspect of using a fume extraction gun, consider working with a trusted welding distributor, certified industrial hygienist and/or the gun manufacturer to address any questions or concerns.
Fume extraction guns can provide results
In combination with many other variables in the welding operation — wire selection, specific transfer methods and welding processes, welding operator technique, and base material selection — fume extraction guns can help companies maintain compliance with safety regulations and create a cleaner, more comfortable welding environment. Proper use and maintenance of the equipment is important to get optimal results.
Learn more about the Bernard® Clean Air E™
New industry standards from the Occupational Safety and Health Administration (OSHA) are protecting employees against potential health hazards in the workplace. These regulations, which dictate allowable exposure limits of welding fumes and other particulates (including hexavalent chromium), have led many companies to invest in fume extraction equipment. An increased desire to maintain optimal welding operator safety and to attract new skilled welding operators to the field is also a consideration in investing in this equipment — companies want to create the most comfortable and healthy work environment possible. The Clean Air E™ MIG fume extraction gun, as shown here, operates by capturing the fume generated by the welding process right at the source, over and around the weld pool. With interchangeable shroud options to help customize your extraction for your application. Some companies may opt for centralized fume extraction systems, which are designed to protect the entire shop area. These systems involve the installation of new ductwork and can be a costly investment for capturing fume particulate in the air. Fume extraction guns are available in a variety of amperages, cable styles and handle designs. As with any welding equipment, they have their advantages and limitations, best applications, maintenance requirements and more. In combination with many other variables in the welding operation; welding wire selection, specific transfer methods and welding processes, welding operator behavior and base material selection — fume extraction guns can help companies maintain compliance with safety regulations and create a cleaner, more comfortable welding environment. Fume extraction guns operate by capturing the fume generated by the welding process right at the source, over and around the weld pool. Various manufacturers have proprietary means of constructing guns to conduct this action, but at a basic level they all operate similarly: by mass flow, or the movement of material. This movement occurs by way of a vacuum chamber that suctions the fumes through the handle of the gun, into the gun’s hose through to a port on the filtration system (sometimes informally referred to as a vacuum box) like the Miller FILTAIR® 215 High-Vacuum Fume Extractor. The welding fumes that these guns remove are composed of a combination of the filler metal and base material. Some fume extraction guns feature adjustable extraction control regulators at the front of the gun handle, which allow welding operators to increase suction as needed (without affecting shielding gas coverage), while others provide this function internally. Regardless of the manner, the ability to balance between the downward flow of shielding gas and the upward flow of the suctioned air is critical. The fume extraction gun needs to provide the appropriate amount of shielding gas to protect the weld from defects such as porosity, without sacrificing the ability to suction fumes efficiently enough to protect the welding operator. The balance allows the weld pool time to react and solidify, and gives the fume particles time to decelerate so they are easier to extract. Typically, fume extraction guns are larger than regular welding guns and tend to be bulky due to the vacuum and hose necessary to extract the fumes. For that reason, some manufacturers create fume extraction guns with a vacuum hose swivel on the rear of the handle to make them easier to maneuver. Manufacturers have also, since fume extraction guns were first introduced (in the late 1960s and early 1970s), found ways to engineer internal components to minimize the handle weight in order to reduce operator fatigue. Fume extraction guns are well-suited for applications using solid welding wire and those in confined spaces. These include, but are not limited to applications in the shipbuilding and heavy equipment manufacturing industries, as well as general manufacturing and fabrication. They are also ideal for welding on stainless steel applications, as this material generates greater levels of hexavalent chromium, and on mild and carbon steel applications. The guns also work well on high amperage and high deposition rate applications and are available, typically, in 300 to 600 amp ranges. Fume extraction guns attach to a localized filtration system, as shown here. Fume removal occurs by way of a vacuum chamber in the fume extraction gun that suctions the fumes through the handle of the gun, into the gun’s hose through to a port on the filtration system. For the best results, fume extraction guns should be used for in-position welding, such as on flat butt welds. In this position, they can most effectively capture fume particles as they rise from the weld pool. In out-of-position welds, the energy of the fume particles causes them to rise at a high rate, making it more difficult for the fume extraction gun to draw them downward and through the vacuum hose. One distinct advantage to fume extraction guns is that they remove the fumes at the source. This will minimize the amount that enters the welding operator’s immediate breathing zone. As with any piece of welding equipment, fume extraction guns benefit from preventive maintenance. Caring for them is similar to caring for a standard GMAW gun. Regularly check for tight connections throughout the length of the fume extraction gun to ensure good electrical flow. Minimizing electrical resistance helps ensure consistent weld quality and prevent premature failure of the front-end consumables — contact tip, nozzle and diffuser. Frequently inspect the nozzle and contact tip for signs of spatter build-up, too, as such build-up can obstruct shielding gas flow and cause weld defects that ultimately will need to be reworked. Spatter build-up can also cause consumables to fail prematurely. Replace the consumables if spatter build-up appears or clean them according to the manufacturer’s recommendation. In some cases the shroud that surrounds the nozzle may also have to be replaced or cleaned free of spatter. To ensure optimal fume extraction capabilities, inspect the vacuum hose regularly for damage, including cuts or kinks that could lead to loss of suction. Replace a damaged vacuum hose as necessary and dispose of it according to the manufacturer’s and/or an industrial hygienist’s directions. Visually inspect the handle for cracks or missing screws, and also check that the gun’s trigger is not sticking or otherwise malfunctioning. Replace or repair these components as necessary. Finally, maintenance on the liner is also important. As with the vacuum hose, use compressed air to clear out any potential blockages during welding wire changeovers or when removing the wire from the gun. Spending an extra few minutes clearing out any debris from the liner can save considerably more time than troubleshooting the weld defects and equipment problems that can result from blockages. Also, track the amount of time that it takes for a liner to wear during the course of the welding operation. Replace the liner prior to that in the future to prevent downtime for replacement during shifts or problems with wire feeding or quality. When in doubt about maintenance or any other aspect of using a fume extraction gun, consider working with a trusted welding distributor, certified industrial hygienist and/or the fume extraction gun manufacturer to address any questions or concerns. Proper use of this equipment can help provide optimal results, and improve the safety and comfort of the welding environment. You may have noticed a material improvement of the cable cover installed on all Bernard® Clean-Air™ fume extraction MIG guns. The new cable cover is more lightweight than the previous cover and allows greater flexibility of the hose assembly. Our replaceable cable cover hose protects from the damage that might be incurred on a hot workpiece, as well as extending the life of the hose for the Clean-Air fume MIG gun assembly. For questions or more information, contact your local ITW sales representative. Effective immediately, to simplify the ordering process on Bernard® Clean-Air® fume exhaust MIG guns, we have replaced the two parts needed to complete the complete the body assembly and vacuum tube assembly into one fume extraction neck assembly part number as shown in the chart below: For questions or more information, contact your local ITW Representative To continue delivering sustainable value to our customers, we regularly assess our product offering to ensure focus and opportunities to innovate our product portfolio. Please be advised that, effective May 1, 2024, we are removing all TOUGH LOCK™ consumables and AutoLength pin options from our robotic, fixed automatic and cobot MIG gun configurators. It is important to note the following: Impacted configurators are listed below: If you have further questions or would like more information, please contact your local ITW representative. We are proud to announce that effective immediately, a new 450-amp self-shielded FCAW series has been added to the Bernard self-shielded FCAW gun portfolio. The new IronPro™ self-shielded FCAW gun is ergonomically designed to provide excellent access and maneuverability in hard-to-reach weld joints and is ideal for rough use in harsh environments. The IronPro self-shielded FCAW guns also feature AccuLock™ S consumables to keep you welding in tight positions longer, with less contact tip changes and less troubleshooting. Features and Benefits: We are pleased to announce that on March 1, 2024, we started offering XS180 and XS260 TGX (10’ and 15’) MIG guns with Bernard neck, silver color (part number 205-60) and AccuLock™ S consumables with Bernard® conventional liner. To continue delivering sustainable value to our customers, we regularly assess our product offering to ensure focus on customer needs and opportunities to innovate our product portfolio. Accordingly, as of March 1, 2024, we have discontinued the XS300, XL300 and XL400 amp TGX air-cooled MIG guns. We are recommending our 200-amp Bernard BTB MIG guns to replace XS300, XL300 and 300-amp Bernard BTB Mig guns to replace XL400 amp TGX air-cooled MIG guns. NOTE: We will continue to support all XS180 and XS260 TGX air-cooled MIG guns. In effort to maximize efficiencies and continue to focus on delivering sustainable value to our customers, effective December 20, 2023, we will be discontinuing a variety of reamer stands due to low demand and sales volume. TOUGH GUN® reamer stands are still part of our product portfolio and will remain available, in heights between 18 and 36 inches in 6-inch increments. As part of our ongoing commitment to continuous improvement, beginning in February 2024 customers will begin to notice that Tregaskiss® cutter blades are coming with a pre-installed washer which is secured and held in place by an o-ring. This incremental improvement provides more convenience for customers by ensuring the washer remains securely in place and gets properly re-assembled when the cutter blade needs to be removed or replaced. Effective February 5, 2024, this modification will be rolled out as a running change across our complete lineup of cutter blades. There will be no change to cutter blade part numbers, but please note that packaging will change to accommodate the addition of the washer. Effective February 20, 2024, as part of our ongoing commitment to continuous improvement, we are making a change to the unicable used on our Tregaskiss® BA1 cobot air-cooled MIG guns. The new unicable better addresses customer needs for a lighter more flexible cable in their cobot welding applications. It is important to note the amperage rating of the BA1 cobot MIG gun will change from 385-amp to 350-amp with mixed gases at 100% duty cycle (ratings are based on tests that comply with IEC 60974-7 standards). There will be no change to configured BA1 gun part numbers, but BA1 replaceable unicables are changing and will have the following new part numbers: If you have any questions regarding this change, please contact your local ITW sales representative. Effective immediately, you will notice two differences on the neck body for all Bernard BTB MIG Guns with a T and C series handle configuration. This will be a running change as we deplete the current inventory of the old-style neck body. If you have questions, please contact your local ITW representative. Improvements have been made to the dedicated motor lubricator on Tregaskiss® TOUGH GUN TT4A and TT4E reamers. Effective immediately, all new TOUGH GUN TT4 reamer orders will come equipped with the new lubricator, without any impact to the reamer part number. However, it is important to note that if ordering the lubricator separately, the part number has changed from TT4-LUB to TT4-2250. New TT4-2250 motor lubricator enhancements: Same mounting footprint, no special adaptors needed. If you have any questions regarding this change, please contact your local ITW sales representative. Regardless of your skill level, you need to make sure that the equipment you use, works as hard as you do. Consider these components of your welding system to help weld conistency. Could it be time to take a good look at your equipment? Read our article published in the November issue of Fabricating & Metalworking. Learn how to recognize the key nuances between two welding-automation options, robots and cobots and how knowing these differences are essential to attain positive results. Have you ever wondered about the differences between robots and cobots? Learn more! “Choosing Between Robots and Cobots for Robotic Welding” in Metalforming Magazine South Louisiana Community College (SLCC) has made a game-changing decision to enhance its welding education program by incorporating Bernard semi-automatic welding guns and AccuLock consumables into its classrooms. This shift marks a significant departure from the MIG guns and consumables they had been using for decades. The transition began within the last year after SLCC’s welding technology instructors began noticing some challenges the students were facing with the welding guns and consumables that they were using. They noticed it took students 20 minutes to change a liner with their current welding guns and consumables. Enter Bernard. After meeting with the instructors and listening to their pains points and need for improvement – Bernard configured a lightweight MIG welding gun with the AccuLock S dual-locked liner consumable system to test in the classrooms. Instructors and students immediately saw the benefits. The AccuLock S dual-locked liner system makes liner installation error-proof by eliminating the guesswork and potential errors that can occur when trimming a liner. More importantly, it maximized their limited time in the classroom. The superior performance of AccuLock contact tips stood out most. SLCC saw a remarkable 50% improvement in tip life compared to the products they were using previously. AccuLock contact tips lasted twice as long. The school found the benefits of using Bernard’s MIG welding guns and AccuLock S consumables for instructional purposes were clearly evident. The lightweight and durable design, coupled with the extended consumable life delivered a substantial return on investment. Not only does the switch to Bernard provide cost savings, but it also equips inexperienced welders with the tools that can withstand the rigors of training and real-world applications. October 23, 2023 In effort to consolidate and simplify packaging and shipments, please note that effective immediately, customers who order a TOUGH GUN TT4 reamer robotic nozzle cleaning station configured with a wire cutter will no longer receive their wire cutter in a separate package as part of their shipment. The wire cutter unit is now being included inside the same single box with the reamer. Affected Part Numbers: If you have any questions regarding this change, please contact your local ITW sales representative. To continue delivering sustainable value to our customers, we regularly assess our product offering to ensure focus on customer needs and opportunities to innovate our product portfolio. Accordingly, due to low demand, as of October 1, 2023, a complete list of discontinued products is now available. Click here to download the complete list in PDF format. Estimated reading time: 7 minutes Speed, accuracy, repeatability — welding automation boasts some big benefits. Using robots across a myriad of manufacturing applications has been a boon to the welding industry, but it hasn’t come without its fair share of misconceptions. Accepting those misconceptions could actually negate those big benefits — and no one has the time (or money) for that. Here are some common myths heard ’round the manufacturing floor — and where we land on them. There seems to be a halo effect around the word “anti” — if it’s anti-“something,” it’s often assumed that the more you use, the better off you’ll be. In welding, that’s not necessarily the case. Using too much anti-spatter spray can actually cause more problems than it solves. When applying it to hot consumables, spraying just enough for it to dry on contact will create a sacrificial barrier that spatter won’t stick to as easily. If the solution is applied to the point where it’s dripping from the torch, it’s too much — and the excess spray will leak all over the parts and weld cell, leading to compromised weld quality, a messier weld cell and premature failure of the torch parts/consumables. Some operators will “dip” the consumables into a cup of the anti-spatter instead of spraying it, but this is also problematic because excess solution can cause the nozzle to become saturated and fail prematurely. When welds are off location, there’s usually an underlying issue that’s causing the problem. Tip bore wear, variations in stamping batches or parts being misaligned due to tooling/spatter can all create a situation where welds are off location. Here, reassessing TCP can help determine what the root problem is rather than just blaming the torch and touching up points. Apply only enough to get the job done. Tips to keep in mind when applying anti-spatter solution include: Contact tips can be the difference-maker between running an efficient welding process and accruing unwanted downtime. For smaller wire sizes in semi-automatic (or handheld) welding, using a contact tip that matches the size of the wire often leads to the desired results. However, in larger industrial operations where robotic welding is common, wire package size (vs. wire size) becomes more of the determining factor for selecting the proper tip size. Large-scale operations often use 1,000–2,000-pound drums or spools as the go-to options due to their high-volume output needs. The connection between the wire and the contact tip needs to be optimized for the tip to last as long as possible, which may require deviating from matching the tip and wire size. The adage goes, “You get what you pay for,” and that sentiment can definitely impact the quality of the work in welding. Investing in robotic welding equipment can add up quickly, so if there’s an opportunity to save a few bucks along the way, selecting a cheaper alternative seems like an appealing option. However, those savings often come at the expense of sacrificing product performance and weld quality, while creating more downtime. The issues experienced during the welding process will show in the end result, along with the bottom-line burn of frequent (and costly) consumable changeovers and excessive downtime for troubleshooting issues. Selecting high-quality, long-lasting consumables over cheaper alternatives will help reduce overall operating costs in the long run because it increases throughput while reducing inventory and downtime. Well … not necessarily. If the contact tip fails and you replace it, you can consider the problem “solved” for at least a short time. However, if the tip keeps failing quickly, it’s safe to say that there’s a greater issue at play. Many factors can cause a tip to fail, including feeding or grounding issues. In those cases, if you put a new tip on, you’re inevitably just waiting until it fails again because you’re not addressing the root cause. If you’re going through tips at a high rate, this is the time to assess your operation and make sure that the drive roll tension is correct and/or the liner is trimmed properly. These are two common issues that can easily cause excessive “burn backs”/tip failure. Choosing the right drive roll style and size for the wire being used is key to smooth and consistent wire feeding. However, if the tension is too high, or too low, it can diminish productivity, quality and efficiency. Tension that’s too tight can deform the wire, resulting in arc instability or burn backs (and too little tension can cause the wire to slip). If the system constantly needs more tension to push wire through, it likely means something else within the system is failing. For example, debris buildup in the liner can inhibit the right tension setting from being effective. To help mitigate the need to crank up the tension, make sure it is set correctly each time the wire spool/drum is changed. Additionally, be sure that the inlet guides are clear/not worn and clean the drive roll surfaces with a wire brush periodically to help maintain proper wire feeding. This is another instance where the idea of “more is better” can be misleading. You definitely need enough gas to cover the weld pool, but turning up the gas doesn’t necessarily result in less porosity — in fact, it could create turbulence and MORE porosity. Proper gas coverage is based on flow, not pressure. If a system isn’t set up properly and the nozzle gets blocked with too much spatter/debris, there won’t be sufficient gas volume (flow) to protect the pool. Leaks in the gas system or excess air flow within the weld cell can also impact the coverage of the weld pool, regardless of how high the gas flow rate is set. Instead of just defaulting to increasing the flow, do a quick run-through of the robotic system to verify that there is a proper tip-to-work distance and that the rest of the system is configured and running correctly. In many applications, weld locations are extremely important. Even though the robot is physically going where it’s programmed to go, if the wire isn’t placed in the joint properly, it could be detrimental to the end product. When welds are off location, there’s usually an underlying issue that’s causing the problem. Tip bore wear, variations in stamping batches or parts being misaligned due to tooling/spatter can all create a situation where welds are off location. Here, reassessing TCP can help determine what the root problem is rather than just blaming the torch and touching up points. Avoiding these common missteps in robotic welding will help you maximize uptime and throughput while minimizing costs — a win from start to finish. Written by Ryan Lizotte (ryan.lizotte@tregaskiss.com), Technical Services Manager, Tregaskiss. September 20, 2023 In order to ensure focus on opportunities to innovate our product portfolio and continue delivering sustainable value to our customers, the changes identified below will be made to the Tregaskiss® 600 amp robotic water-cooled MIG gun offering effective September 29, 2023. The gun housing of 600 amp robotic water-cooled MIG guns not equipped with wire brake will feature a wire brake plug (part number RW16-WBP). This change will also allow customers to install wire brake at a later date with the appropriate wire brake kit without having to change the gun housing. There will be no change to MIG guns equipped with wire brake. Additionally, due to low demand, please note that all 45-degree neck and 0.035” (0.9 mm) wire size options will be removed from the 600 amp robotic water-cooled MIG gun configurator. If you have questions or need assistance with regard to these changes, please contact your local ITW welding sales representative. Estimated reading time: 5 minutes Self-shielded flux-cored welding is frequently used for structural construction and other jobsite welding since it offers a significant productivity advantage compared to stick welding. Welders using this process are likely holding their welding guns for much of the day, and they may be standing on elevated girders or lifts trying to get into tight places to complete a weld. Because of this, it’s important to choose a self-shielded flux-cored gun that is comfortable, lightweight and maneuverable to help get work done efficiently. Here are several key factors to consider when selecting a self-shielded flux-cored welding gun and tips for properly maintaining it to optimize performance. Not every welding gun fits every application. They come in various amperages and configurations, with features that include heat shields, configurable necks and adjustable cable lengths. The key is finding a flux-cored gun that works for each welder, since many options come down to operator preference. Guns rated at 350 or 450 amps are common in structural field welding applications. Guns rated at 600 amps are also available but used less often due to being heavier. It’s important to avoid undersizing the welding gun since it can lead to overheating and other problems. When selecting the gun amperage, consider the wire sizes that will be used most often. Typical wire sizes for a 350-amp gun are 1/16 inch and smaller. Wire sizes for 450-amp guns are 0.72 inch and larger, including 5/64 and 3/32 inch. Some self-shielded flux-cored guns are available with either a replaceable cable liner or a fixed cable liner. The demanding environments where self-shielded flux-cored welding takes place can be hard on the gun and consumables, so replaceable liners provide benefits. They offer quick and easy cable maintenance and can extend product life, since welders can change out components that have high levels of wear. Guns with replaceable liners also tend to have a lighter weight cable and provide more flexibility to weld around edges or corners. Guns with fixed cable liners are often larger, which can be an issue when welding in tight spaces. The cables are also typically stiffer and more rigid, so they can take more abuse. Once a fixed cable liner has reached the end of its useful life, the entire gun must be replaced. Gun necks are available in varying lengths and bend angles. The choice for the application often comes down to operator preference or weld joint access and configuration. A slimmer neck provides a better view of the weld pool and improved access to tight areas. A shorter neck typically provides more control compared to a longer neck. Still, operators may prefer a longer neck to increase the distance between themselves and the heat of the weld puddle — especially in higher amperage applications. Keep in mind that lightweight, rotatable necks help reduce operator fatigue by aiding with posture and positioning, and they improve weld visibility. In the field, triggers that get wet or covered in dirt still need to work, so it’s important to purchase a quality gun that includes a durable trigger. Look for a gun with an enclosed trigger. This protects the contacts inside a housing, so the trigger is less prone to wear and breakage. If you’re using a replaceable cable liner, it may have an internal or external trigger lead. Be aware that external trigger leads may require more maintenance because they can easily get snagged or catch on things like bolt heads. However, they are typically quick and easy to replace. A handle needs to be rugged and durable for the jobsite, but it should also feel comfortable in the operator’s hand. A self-shielded flux-cored gun with an optional dual schedule switch allows for wire speed adjustment while welding. In some guns, this switch is integrated into the handle to keep it protected from spatter. The ability to toggle between weld parameters easily—without having to stop welding and change settings—saves time and improves productivity. Beyond choosing the right gun for the job, it’s also important to use and maintain it properly. Consider these tips for optimizing gun performance. Store and handle it properly: Jobsites can be dusty, dirty places. Be sure to store guns and cables properly when not in use. Roll the cables up and put the gun away in a clean, dry place so there’s less risk it will be damaged. Maintain it as needed: Keep the gun and all components clean and check all connections periodically. Loose connections can cause electrical resistance and heat buildup, which can result in premature wear. Take the time to regularly blow out the liner with clean, compressed air to remove dirt and debris. Immediately address any damage to the gun components with maintenance or replacement. Invest in quality consumables: Consumable choice often comes down to cost or operator preference. However, investing in high-quality consumables can help extend the life of the gun, provide better performance and reduce downtime for changeover. The self-shielded flux-cored process can deliver significant benefits for productivity and efficiency. Choosing the right gun and components—and maintaining them properly—plays a key role in optimizing your results. Written by Stephen Bennett (stephen.bennett@bernardwelds.com), Mechanical Engineer, Bernard, Republished with permission from Modern Contractor Solutions (August, 2023) September 5, 2023 Effective September 29, 2023, the 350 amp MA1 fixed automatic MIG gun will be removed from the Tregaskiss product portfolio and will be replaced with the existing equivalent 385 amp MA1 fixed automatic model. This initiative allows us to focus on delivering our best quality solution to our customers. The only differences between the 350 amp and the 385 amp models are as follows: Affected Part Numbers: Replacement Gun Options: If you have any questions or need assistance with regard to these changes, please contact your local ITW sales representative. Today, even the smallest weld shops are making the jump to robotics, and even the largest, highly automated OEMs likely have semiautomatic weld cells for repairs or for welding parts that don’t lend themselves to automation. In automotive manufacturing, these manual cells may be midway through the line for welding frames or at the end for minor rework. If you’re in heavy equipment manufacturing, you might automate multipass welding on thick parts and reserve semiautomatic welding for tacking the parts or adding specialized components. No matter your industry or your level of welding automation, an effective weld cell layout can help. Work needs to flow in an orderly fashion. Power, grounding, and wire feed cables need to be properly managed. And, of course, you need to ensure welders can work safely, consistently, and with good ergonomics. Proper layout supports high productivity and quality, along with cost savings. Whether robotic or semiautomatic, a well-designed weld cell makes efficient use of available space, where every component—the power source, welding gun, weld table, cables—ensures parts can be produced with little interruption. Streamlining workflow is a good first step. This involves setting up equipment in a way that helps operators avoid handling parts multiple times. Double handling of parts adds non-value-added seconds to the overall manufacturing cycle time and reduces the capacity for completed parts sent out the door. Think with an assembly line mentality. Look beyond the weld cell to how parts are being delivered. For example, when an operation requires that parts receive semiautomatic tack welds before robotic welding, work must flow at a consistent pace to prevent the welding robot from sitting idle. To ensure a steady supply of parts and prevent bottlenecks, the cell should have a single point of entry. For optimal workflow, parts should move out of the weld cell in the same direction. Minimize the distance a part needs to travel by keeping assembly points close together. Weld cells contributing to the completion of a single weld assembly should be in the same area of the facility. This proximity not only reduces time for moving a part, but it also lessens the number of footsteps operators need to make. Excessive movement in a welding cell is considered non-value-added work. If you notice bottlenecks or operators or welding robots standing idle, or operators walking too far between weld cells, you might consider performing an audit. Any idle operation results in a failure to capitalize on the investment of that process. An audit can help you identify the causes behind these problems and implement solutions. The aim is to balance out the operations so that every aspect contributes to value-added work and high productivity. Welding ergonomics are at the center of a semiautomatic welding cell layout. A more comfortable, healthier welding operator is a more productive one. Setting up the weld cell in a way that minimizes the need to reach repetitively or move awkwardly can reduce the risk of work-related musculoskeletal disorders. Try to position the workbench or workpiece between the welding operator’s waist and shoulders, since this promotes a neutral posture that reduces stress on the body. When welding large components, use positioners or weld tables that move or rotate the part to the correct height and angle. The same holds true when providing operators with a MIG gun that suits them, whether it be a curved or straight handle. Locking triggers help support comfort, as do rubber mats to stand on. Strategically locating the power source and wire feeder can make the cell more efficient. Keep the two pieces of equipment as close as possible, so the operator can easily access them. Close proximity allows for shorter power cables for smoother wire feeding and also reduces electrical resistance drops so welding parameters remain more consistent. Keep ground cable connections to a minimum. Some companies string together welding cables between weld cells for the same power source. This practice is inefficient, however, and can lead to problems. The multiple junctions can wear out easily, which causes electrical resistance and poor weld quality over time. The electrical resistance also can shorten consumable life, resulting in erratic arcs and burnbacks, leading to more downtime for contact tip changeovers. Implementing an effective robotic welding cell layout requires careful planning and attention to detail. One of the best approaches is to test the layout through virtual modeling or 3D simulation. These software programs can simulate the welding gun configuration—neck length, nozzle, and mounting (solid versus clutch)—to ensure it will operate properly within the work envelope. They also consider weld sequencing, robot arm movement, fixturing, and the parts to be welded so that you can be confident everything will work as planned. Take the time to simulate the weld cell layout and process before equipment integration to avoid issues once the welding robot is in service. Simulations help prevent downtime during mass production for troubleshooting and potential expenses for revamping tooling or replacing components. They also can model another key factor—welding robot reach. Be sure to match the size of the part with the reach of the robot. The robot must be able to reach all weld joints on the part; otherwise, you might need multiple robots for the application. A single, small welding robot won’t suffice for welding on a large part. If you have a weld on the edge of the reach envelope, you might not be able to achieve the optimal welding gun angle to create quality welds. This can add costs for rework, and you’ll likely need to replace stretched power cables that fail prematurely. Regarding tooling, you might be tempted to purchase less expensive options—though such tooling might not have the features you need, such as the appropriate number of clamps or location pins. This can lead to inconsistent part fit-up or locating that requires multiple passes to fill the weld joint, adding to cycle time. You might experience more downtime as you reprogram the welding robot to accommodate the gaps, or you may end up needing to invest in touch sensing to locate the joint. Even worse, you might need to upgrade your tooling after the initial design phase—a costly step. Also consider the positioners. Their size and weight capacity must account for both the weight of the part and the tooling. Design the robotic cell for the heaviest part to be welded. Where you place the power source and wire feeder matters as they both impact power cable management and grounding. If space is at a premium, you may want to place the welding power source above the robot cell on a mezzanine. This way, you can run the power cable and ground leads down channels in the cell’s back wall directly to the tooling and welding robot. These leads are stationary—except for the ones on the robot, so be sure to account for the robot’s air movements to minimize wear on the cables. Placing a junction power block at the base of the robot and running a high-flex power cable from that base up to the wire feeder can help save time in repairs, and it can save money. If the high-flex cable becomes worn, you just replace that shorter piece instead of the entire cable. The same approach works for the grounding leads. Finally, determine the best location for the nozzle cleaning station or reamer. This peripheral cleans the nozzle of spatter during routine pauses in welding. It helps extend consumable life and reduces downtime for changeover. The reamer needs to be close enough for the robotic welding gun to engage fully for the ream cycle. If you’re operating two robots close together, you can program them both to use the same reamer. Avoid mounting the reamer anywhere but a flat surface, since positioning it at an angle can cause anti-spatter to leak over equipment or fixtures. Avoid interrupting the weld cycle by cleaning the nozzle during robot idle time. For example, consider cleaning the nozzles while parts are being transferred in and out of the fixture or while components are being loaded into a weld cell. If you’re experiencing bottlenecks or missing productivity or quality goals, take a look at the welding cell layout. In a semiautomatic setup, never overlook welder comfort and safety. In a robot cell, moving power cables, power sources, wire feeders, or anything else can change how much that cell can produce over a shift. The little things matter, and missing just one detail can snowball into bigger problems down the road. Small changes can make a big impact on the efficiency you can achieve. Written by Justin Craft (justin.craft@bernardwelds.com), Field Technical Services Specialist, Tregaskiss and Bernard, Republished with permission from The Fabricator (August, 2023). Estimated reading time: 6 minutes The welding gun is a vital piece of equipment in a robotic welding system, serving as the conduit for the welding wire, gas, and power. However, it can sometimes be an afterthought when companies implement an automated welding solution. Unfortunately, this oversight can lead to a host of problems, not to mention frustration. That is especially true for first-time users making the investment. The wrong robotic welding gun can also cause issues for those more experienced with robotic systems. It’s not uncommon for companies to purchase the same gun for a new robot and tooling when, in fact, it may not be the best option. Companies also need to determine their welding amperage and arc-on requirements for the application. This ensures that they purchase a robotic welding gun with the proper duty cycle — the amount of welding that can occur at a rated output over a period without causing damage to the gun. Robotic welding guns are available in a variety of ratings, including air-cooled models that operate at 350 or 385 A at 100% duty cycle. Today, most robotic welding systems are through-arm models in which the power cable runs through the casting of the robot arm. As a first step in configuring a robotic welding gun for these systems, it’s important to know the make and model of the robot, power source, and wire feeder. Each equipment manufacturer has a different interface that dictates how each piece of equipment connects with one another. There are higher amperage water-cooled options, which are typically 400 A and above, available in the marketplace. Some of these may be rated at 100% duty cycle, while others are rated at 60%. Don’t be fooled by high amperage unless it’s at 100% duty cycle. Hybrid options are available for companies that want the simpler construction of an air-cooled robotic welding gun with the added cooling capacity of a water-cooled one. These guns have external water lines that circulate water around the nozzle to keep the front-end consumables cooler. For a robotic welding gun to access the weld joints, it’s critical that the work envelope is adequate. Companies need to consider not just the size of the gun but also the space that is available when the tooling, fixtures, and parts are all in place. Joint design and weld sequencing also factor into the equation. It’s important that there is room and time for the welding gun to weld the joints in a sequence that keeps heat to a minimum. Companies should avoid heat soaking the parts, so they don’t become distorted. A robot integrator can conduct a 3D simulation using models provided by the robotic welding gun manufacturer through computer-aided design (CAD) to make sure the gun and neck have the proper access and reach within the given space. The CAD model can also show whether the selected gun has the correct tool center point (TCP) and can extend to the nozzle cleaning station for reaming or to a service window for consumable changeover. A service window supports safety in the operation by eliminating the need for an employee to physically enter the cell. Some robotic welding gun manufacturers offer online configurators that allow companies to customize the equipment for their exact application. These configurators guide the user through a step-by-step process, providing options to choose from for each component. With or without this tool, companies need to consider what their needs are based on their upfront assessment. Gun mount: There are two mounting options for a robotic welding gun to protect it in the event of a collision — a solid arm mount and a clutch. If the robot or end user’s safety procedure requires external collision detection, a clutch can be added to the system. This component functions both mechanically and electrically by recognizing a collision and sending a message to the robot controller to stop the system. If procedures allow for reliance on only the robot’s collision detection, then a solid mount will suffice. Neck: The neck length and angle must provide the approach angle to weld parts properly and to allow for smooth wire feeding. Standard neck angles are 22, 45, and 180 deg. Through-arm robots generally use a 45-deg neck; however, that should be verified with the CAD model/simulation before implementing. Companies will also need to take into consideration the welding wire they are using. For example, aluminum wire requires a straighter neck to feed through properly since it is so soft. Welding cable: For through-arm robots, the make and model dictate the cable length. For conventional robots (where the cable assembly runs outside the robot arm), the gun cable length also depends on the robot make and model along with the location of the feeder. It may be remotely mounted or mounted on the robot itself. There is more flexibility with cable length for these robots, but it’s important not to use too long of a cable since this can lead to wire-feeding issues. Conversely, a cable that is too short can stretch and break down quickly. Welding consumables: When choosing contact tips for the robotic welding gun, look at the welding process. Pulsed gas metal arc welding (GMAW-P), for example, is quite hard on contact tips due to its high-frequency waveforms. This process requires a harder tip or a contact tip specifically designed for pulsed welding. The chosen nozzle needs to allow proper access to the weld joint. A tapered nozzle works well when using smaller-diameter wire and contact tips. Higher-premium consumables are a good choice since these last longer and reduce downtime and labor for changeover. Welding supervisors and operators should schedule time to perform preventive maintenance, such as checking connections and visually inspecting consumables for spatter, during routine pauses in welding. Liners are another factor to consider, and the welding wire being used affects the choice. Flux- and metal-cored wires tend to be stiffer and harder to feed than solid wires. They require an extra-heavy-duty liner to support the wire and gain smooth feedability as it moves toward the contact tip. A D-wound galvanized wire works well. Companies can also use this liner for solid wire with good success. Companies invest in robotic welding systems to increase quality, productivity, and cost savings through a fast, repeatable process. To gain those benefits, every part of the system needs to be functioning optimally. Ensuring that the robotic welding gun has been configured properly before implementing the system can prevent downtime and extra expenses. This article was written by Ryan Lizotte (project manager, Tregaskiss, Windsor, Ontario, Canada) for the American Welding Society.Fume Extraction Guns: Understanding the Basics
Fume Extraction Guns: Understanding the Basics
The basics of fume extraction guns
Applications, advantages and limitations
Maintenance tips
PRODUCT UPDATE — Material Improvement for Clean-Air® Fume Extraction MIG Gun Replaceable Hose Cover
PRODUCT UPDATE — Material Improvement for Clean-Air® Fume Extraction MIG Gun Replaceable Hose Cover
PRODUCT UPDATE – Fume Extraction Neck Assembly Part Number Changes
PRODUCT UPDATE – Fume Extraction Neck Assembly Part Number Changes
Description Fume Extraction Neck Assembly New Part Numbers Discontinued Vacuum Tube Part Numbers and Body Assembly Part Numbers 45° neck, medium — handle option T 2390047 2390027 + 1040082 60° neck, medium — handle option T 2390048 2390028 + 1040083 45° neck, medium — handle option N 2390049 2390029 + 1040084 60° neck, medium — handle option N 2390050 2390030 + 1040085 CONFIGURATOR SIMPLIFICATION: Changes to all automation gun configurators
CONFIGURATOR SIMPLIFICATION: Changes to all automation gun configurators
PRODUCT UPDATE — NEW ADDITION TO THE BERNARD FCAW SELF SHIELDED GUN PRODUCT OFFERING
PRODUCT UPDATE — NEW ADDITION TO THE BERNARD FCAW SELF-SHIELDED GUN PRODUCT OFFERING
PRODUCT UPDATE — ACCULOCK™ S CONSUMABLES AND NEW NECK ON XS180 AND XS 260 TGX™ SERIES MIG GUNS
PRODUCT UPDATE — ACCULOCK™ S Consumables and New Neck on XS180 AND XS 260 TGX™ Series MIG Guns
DISCONTINUED PRODUCT – TGX Series MIG Gun Amperages
DISCONTINUED PRODUCT – TGX Series MIG Gun Amperages
DISCONTINUED PRODUCT – Select Reamer Stand Heights
DISCONTINUED PRODUCT – Select Reamer Stand Heights
Part Number Description RST-20 Reamer stand, 20-inch RST-22 Reamer stand, 22-inch RST-23 Reamer stand, 23-inch RST-27 Reamer stand, 27-inch RST-29 Reamer stand, 29-inch RST-32 Reamer stand, 32-inch RST-35 Reamer stand, 35-inch RST-40 Reamer stand, 40-inch RST-45 Reamer stand, 45-inch PRODUCT UPDATE – Washers to Be Pre-installed on All Tregaskiss® Cutter Blades
PRODUCT UPDATE – Washers to Be Pre-installed on All Tregaskiss® Cutter Blades
PRODUCT IMPROVEMENT – BA1 Cobot MIG Guns to Feature Lighter Unicables
PRODUCT IMPROVEMENT – BA1 Cobot MIG Guns to Feature Lighter Unicables
Part Number Description BA1U03S BA1 replaceable unicable, solid mount, 3 ft BA1U03.5S BA1 replaceable unicable, solid mount, 3.5 ft BA1U04S BA1 replaceable unicable, solid mount, 4 ft BA1U04.5S BA1 replaceable unicable, solid mount, 4.5 ft BA1U05S BA1 replaceable unicable, solid mount, 5 ft BA1U05.5S BA1 replaceable unicable, solid mount, 5.5 ft BA1U06S BA1 replaceable unicable, solid mount, 6 ft BA1U07S BA1 replaceable unicable, solid mount, 7 ft BA1U08S BA1 replaceable unicable, solid mount, 8 ft BA1U09S BA1 replaceable unicable, solid mount, 9 ft BA1U10S BA1 replaceable unicable, solid mount, 10 ft BA1U12S BA1 replaceable unicable, solid mount, 12 ft BA1U15S BA1 replaceable unicable, solid mount, 15 ft EBA1U03S BA1 replaceable unicable, solid mount (Euro), 3 ft EBA1U03.5S BA1 replaceable unicable, solid mount (Euro), 3.5 ft EBA1U04S BA1 replaceable unicable, solid mount (Euro), 4 ft EBA1U04.5S BA1 replaceable unicable, solid mount (Euro), 4.5 ft EBA1U05S BA1 replaceable unicable, solid mount (Euro), 5 ft EBA1U05.5S BA1 replaceable unicable, solid mount (Euro), 5.5 ft EBA1U06S BA1 replaceable unicable, solid mount (Euro), 6 ft EBA1U07S BA1 replaceable unicable, solid mount (Euro), 7 ft EBA1U08S BA1 replaceable unicable, solid mount (Euro), 8 ft EBA1U09S BA1 replaceable unicable, solid mount (Euro), 9 ft EBA1U10S BA1 replaceable unicable, solid mount (Euro), 10 ft EBA1U12S BA1 replaceable unicable, solid mount (Euro), 12 ft EBA1U15S BA1 replaceable unicable, solid mount (Euro), 15 ft PRODUCT UPDATE — Change on Neck Body for all T and C Series Handle Configurations on Bernard BTB MIG Guns
PRODUCT UPDATE — Change on Neck Body for all T and C Series Handle Configurations on Bernard® BTB MIG Guns
PRODUCT UPDATE — New Motor Lubricator Enhancements for TOUGH GUN® TT4A and TT4E Reamer Robotic Nozzle Cleaning Station
PRODUCT UPDATE — New Motor Lubricator Enhancements for TOUGH GUN® TT4A and TT4E Reamer Robotic Nozzle Cleaning Station
Five Equipment Adjustments to Improve Weld Quality
Five Equipment Adjustments to Improve Weld Quality
Choosing Between Robots and Cobots for Robotic Welding
Choosing Between Robots and Cobots for Robotic Welding
South Louisiana Community College Chooses Bernard® Semi-Automatic MIG Welding Guns and AccuLock™ Consumables for Welding Education | Customer Testimonial
South Louisiana Community College Chooses Bernard® Semi-Automatic MIG Welding Guns and AccuLock™ Consumables for Welding Education
Packaging Change — Wire Cutter No Longer Packaged Separately When Configured on a TOUGH GUN® TT4 Reamer
Packaging Change — Wire Cutter No Longer Packaged Separately When Configured on a TOUGH GUN® TT4 Reamer
Discontinued Products — Select Bernard® and Tregaskiss® Consumables
Discontinued Products — Select Bernard® and Tregaskiss® Consumables
Understand the Truth About These 7 Robotic Welding Myths
Understand the Truth About These 7 Robotic Welding Myths
Myth 1: The more anti-spatter solution you use, the better the results
Myth 2: Using a contact tip that matches the size of the wire always leads to the best results
Myth 3: The cheapest products will work
Myth 4: Changing the contact tip will always solve the problem
Myth 5: Higher drive roll tension results in better wire feeding
Myth 6: Increased gas flow results in less porosity
Myth 7: Off-location welds are always the gun’s fault
Republished with permission from Fabricating and Metalworking, (October 2023)PRODUCT UPDATE – CHANGES TO THE TREGASKISS® 600 AMP ROBOTIC WATER-COOLED MIG GUN OFFERING
PRODUCT UPDATE – CHANGES TO THE TREGASKISS® 600 AMP ROBOTIC WATER-COOLED MIG GUN OFFERING
Physical changes to the product:
Changes to configurable options:
Self-Shielded Gun Performance
Self-Shielded Gun Performance
1. Flux-Cored Gun Options
2. Amperage
3. Replaceable or Fixed Cable Liners
4. Necks
5. Trigger
6. Handle
The Best Results
Closing Thoughts
PRODUCT UPDATE – 350 AMP MA1 FIXED AUTOMATIC MIG GUNS TO BE REPLACED WITH 385 AMP MA1 MODELS
PRODUCT UPDATE – 350 AMP MA1 FIXED AUTOMATIC MIG GUNS TO BE REPLACED WITH 385 AMP MA1 MODELS
Best Practices For Weld Cell Layout
Best Practices For Weld Cell Layout
The Big Picture
The Semi-Automatic Weld Cell
The Robotic Weld Cell Layout
Small Moves, Big Impact
Proper Robotic Welding Gun Configuration
Proper Robotic Welding Gun Configuration
Configuring the Gun
Maintaining Efficiency