Key MIG Gun Components for Job Performance
MIG welding is a common welding process especially useful for beginner and DIY welders due to its easy-to-learn nature, shorter lead times and lower production costs. The versatility of MIG welding allows users to work on a wide range of materials with less stopping and restarting. The process features a continuous consumable wire electrode being fed through a welding gun and into a weld pool. The gun also feeds a shielding gas alongside the wire to protect the weld pool from contaminants.
While there are different types of MIG guns that have unique parts (e.g., water-cooled, air-cooled, fume extraction), all MIG guns have some parts in common. Understanding the components of a MIG gun and the process by which it works will help you make decisions on the consumables and gun type you select for your job. Here’s what you need to know.
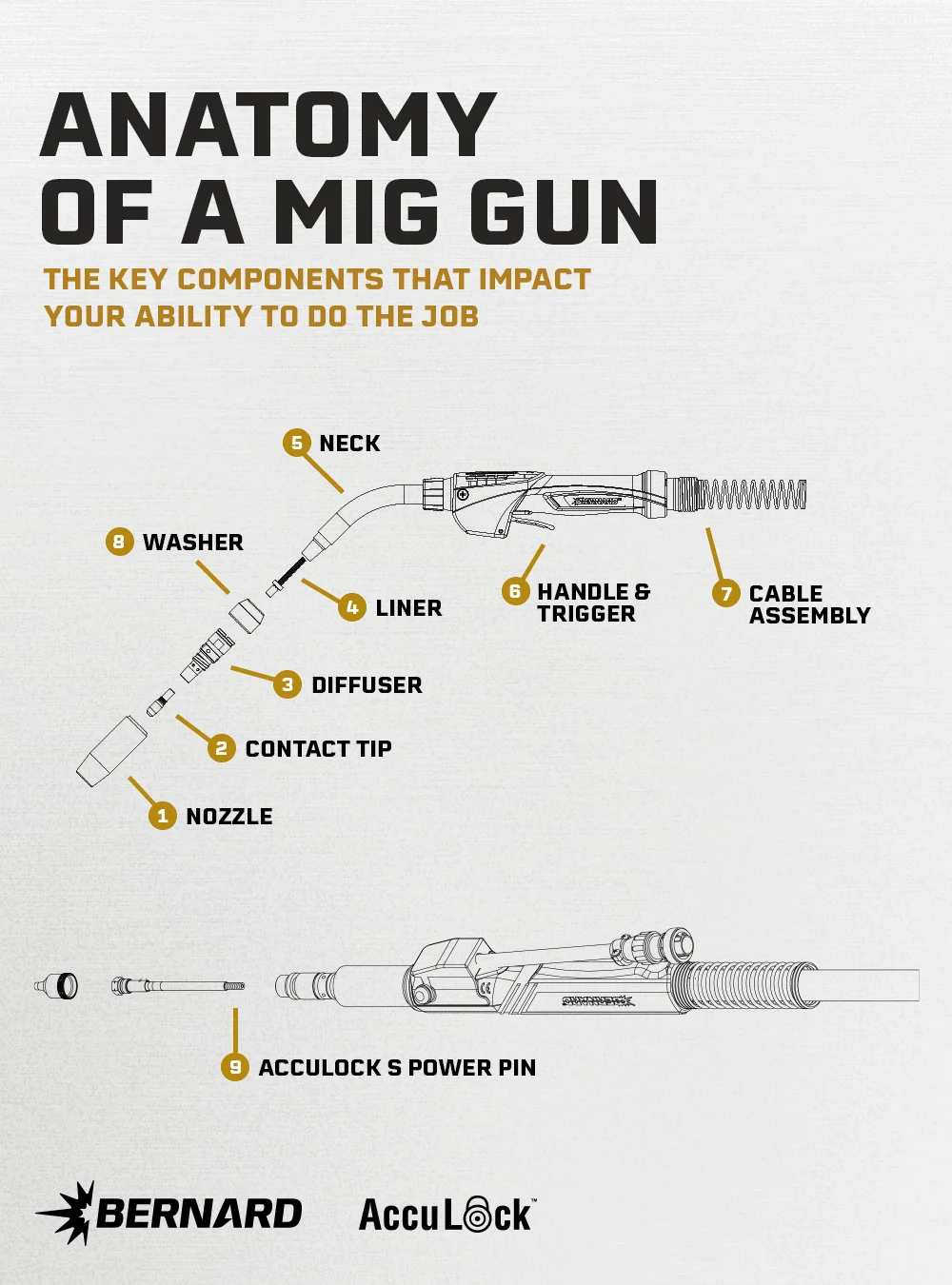
CONSUMABLES
1. Nozzle
- The nozzle directs the shielding gas to cover the weld puddle.
- By shielding the weld puddle, the nozzle helps to prevent spatter on the weld surface while simultaneously protecting internal components of the gun from heat and spatter.
2. Contact Tip
- The contact tip guides the wire and transfers the current from the neck through the filler metal and to the work surface. Consistent wire feeding ensures a stable arc and high weld quality.
3. Diffuser
- The diffuser conducts electricity to the contact tip while dispersing gas evenly across the weld pool.
- Ensuring even distribution of shielding gas ensures consistent coverage of the weld pool, preventing contamination and defects like porosity and oxidation.
4. Liner
- The liner is crucial to MIG welding because it guides the wire electrode from the wire feeder through the cable to the contact tip.
- A worn or low-quality liner can cause friction, leading to inconsistent feeding and arc instability and, ultimately, poor weld quality.
- There are several materials of liners for consideration, each with advantages in different applications.
ESSENTIAL GUN COMPONENTS
5. Neck
- The neck is the front-end extension of a MIG welding torch and houses vital components like the contact tip, gas nozzle and wire feeder inlet.
- It directs the welding arc and shielding gas precisely onto the weld joint, improving weld quality and consistency.
- Selecting the right neck (i.e., long versus short) is important because it impacts a welder’s posture, visibility and heat control.
6. Handle and Trigger
- The handle and trigger impacts how long an operator can weld without experiencing fatigue.
- Handles with an ergonomic design and a natural feeling grip will improve operator comfort and welding duration.
- When selecting a trigger, it needs to be responsive to the touch and best suited for the job (e.g., multi-schedule, locking).
7. Cable Assembly
- In MIG welding, the cable assembly delivers power, gas, filler metal and control signals to the welding gun.
- Without the successful transmission of each of these elements, the weld will not function as intended.
- Compression fittings are an integral aspect of the assembly because they provide a reliable connection, better energy transfer and less resistance.
OTHER COMPONENTS
8. Insulator
- Plays a critical role in electrical isolation and heat management.
- Made of a non-conductive material to help electrically isolate the metal components of the welding gun (e.g., the trigger mechanism) from the electrical circuit carrying the welding current.
- Acts as a thermal barrier between nozzle and trigger mechanism, preventing overheating and malfunctions.
9. Power Pin
- Power pins provide a direct connection for wire, weld power and gas flow between the welding machine and/or wire feeder and the MIG gun. An accurate gun-to-machine connection is critical to ensure that the filler wire, gas and weld power are passed efficiently to the gun.